321026 TE Connectivity, 321026 Datasheet - Page 4
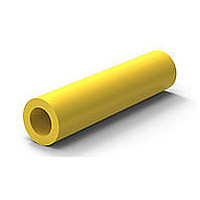
321026
Manufacturer Part Number
321026
Description
SPLICE, BUTT, PLASTI-GRIP, 26-22 AWG
Manufacturer
TE Connectivity
Datasheet
1.321026.pdf
(19 pages)
Specifications of 321026
Color
Yellow
Diameter, Insulation
0.080 in.
Material, Sleeve
Vinyl, UL 94V-0
Splice Type
Butt
Wire Size
26-22 AWG
Product Type
Splice
Sealed
No
Body Style
PLASTI-GRIP
Insulation
Yes
Insulation Support
Insulation Support
Insulation Diameter (mm [in])
2.03 [.080] Max.
Finish
Tin
Wire/cable Size (cma)
202 – 810
Butt Splice Type
Standard
Wire Range (mm [awg])
0.12-0.40² [26-22]
Insulation Sleeve Material
Vinyl
Government/industry Qualification
No
Rohs/elv Compliance
RoHS compliant, ELV compliant
Lead Free Solder Processes
Not relevant for lead free process
Rohs/elv Compliance History
Always was RoHS compliant
Packaging Method
Loose Piece
Lead Free Status / Rohs Status
RoHS Compliant part
3.4. Chemical Exposure
3.5. Wire Selection and Preparation
The terminals and splices will accept solid or stranded copper wire sizes 26 through 1/0 AWG and stranded
wire sizes 8 through 2/0 AWG (509 through 150,500 circular mil area) with an insulation diameter range of 1.27
through 19.69 mm [.050 through .775 in.]. Proper strip length is necessary to properly insert the wire into the
terminal or splice. The strip length of the wire is shown in Figure 2.
3.6. Wire Placement
Stranded wire conductors must be inside the terminal or splice wire barrel. No strands can be folded back over
the wire insulation. Conductor ends must be bottomed in the wire barrel. The wire insulation must be inside the
insulation of the terminal or splice, but must not enter the wire barrel, to provide strain relief for the wire.
3.7. Crimp Requirements
The terminal or splice must be crimped to the wire according to instructions packaged with applicable tooling.
4 of 19
PLASTI-GRIP Terminals and Splices
CAUTION
CAUTION
Do not store terminals or splices near any chemical listed below as they may cause stress corrosion
cracking in the terminal or splices.
Alkalies
Amines
A. Wire Barrel Crimp
The crimp applied to the wire barrel portion of the terminal or splice is the most compressed area and is
most critical in ensuring optimum electrical and mechanical performance of the crimped terminal or splice.
The crimped area must be symmetrical on both sides of the wire barrel of the terminal or splice. The crimp
may be off center on the wire barrel but not off the end of the wire barrel. See Figure 3.
B. Crimp Dot Code
Some tools with multiple crimping chambers will emboss a crimp dot code onto the terminal or splice
insulation when crimped. The crimp dot code must be fully formed on the insulation to indicate that the
correct product and tooling combination was used. The crimp dot code must correspond with the wire size
marking on the tooling. See Figure 3.
C. Wire Conductor and Insulation Location
After crimping, all conductors must be held firmly inside the wire barrel. No strands can be folded back
over the wire insulation. The wire insulation must be inside the insulation barrel of the terminal or splice,
but must not enter the wire barrel. Conductor ends must be flush with, or extend slightly beyond, the end
of the wire barrel; or, in splices with a wire stop inside the center of the splice, conductor ends must butt
against the wire stop. See Figure 3.
D. Terminal or Splice Insulation
The terminal or splice insulation must not be deformed, cut, or show uneven stress marks. See Figure 3.
E. Bellmouth
There shall be no rear bellmouth. The front bellmouth shall be evident as shown in Figure 3.
!
!
Reasonable care must be taken not to nick, scrape, or cut any strands during the stripping operation.
Wire insulation shall NOT be cut or broken during the crimping operation. Reasonable care should be taken to provide
undamaged wire terminations.
Ammonia
Carbonates
Citrates
Nitrites
Tyco Electronics Corporation
Phosphates Citrates
Sulfur Nitrites
Sulfur Compounds
Tartrates
114-2161
Rev C