IHD260 CT-Concept Technologie AG, IHD260 Datasheet - Page 11
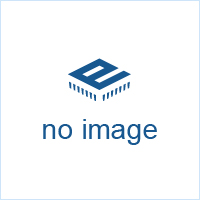
IHD260
Manufacturer Part Number
IHD260
Description
Data Sheet Ihd 260/660 Dual Channel Scale Igbt Driver Core
Manufacturer
CT-Concept Technologie AG
Datasheet
1.IHD260.pdf
(13 pages)
Footnotes
1)
2)
3)
4)
5)
6)
7)
8)
9)
I G B T - D r i v e r . c o m
The unipolar primary supply voltage with a nominal value of V(VCC, GND) = 15.0V is multiplied by
a magnetic transformer, resulting in a unipolar secondary power supply voltage with a nominal
value of V(Cs, COM) = 16.4V. To provide a bipolar gate-driving voltage with the nominal values of
V(G, E) = +15.1V for turn-on and V(G, E) = - 15.1V for turn-off, both gate and emitter are
switched in full-bridge configuration via biploar junction transistors (providing a total nominal level
shift of 1.3V). The primary side is equipped with an automatic power-on reset which clears the
fault memories when the supply voltage approaches a specified limit with a maximum value of
13.5V.
In typical applications (hard-switching topology using recommended gate resistors and gate
charge) the switching frequency is primarily limited by the switching losses of the IGBT module or
by the gate power due to the gate charge required by the module. The switching losses of the
gate driver depend strongly on the particular operating conditions and increase with reducing the
gate resistance and increasing switching frequency. For switching frequencies beyond 10kHz or
gate charges beyond 55μC, the thermal limits of the gate driver may be exceeded. A derating of
the IGBT average gate power is required under these estimated exemplary conditions. Conditions
other than those specified may affect the reliability or lead to thermal breakdown of the gate
drivers. Please ask our support team for a specific estimation. As a rule, the case temperature of
any component of the gate driver should stay below 65°C for an ambient temperature of 25°C.
The total external gate resistance is the sum of the IGBT-internal chip resistances and the
externally used gate resistors. Note that the driver-internal minimum resistance is below 0.2Ω. Due
to the finite slew rate of the driver output voltage and to parasitic inductances in the gate control
loop, however, the resulting gate current may not approach the nominal maximum value of 6.0A.
Equivalent delay, rise or fall times are derived from comparisons with the results obtained when
modeling the driver as an ideal pulse-shaped voltage source with no delay and an infinite slew
rate.
At the REF pin, a 1.5 kΩ resistor is connected to the positive voltage terminal Cs of the secondary-
side power supply in parallel with a nominal 150μA current source. The reference voltage may be
set via an external Zener diode or an external resistor connected to pin E. Furthermore, at pin ME
a 2.2 kΩ resistor is connected to Cs in parallel with a nominal 1.4mA current source. This solution
should be fully compatible with IHD series gate drivers in terms of function and parameters.
Maximum continuous or repeatedly applied DC voltage or peak value of the repeatedly applied AC
voltage
Caution for option C: operating voltages exceeding 600V may degrade the long-term
characteristics of the optocouplers, resulting in an increased delay or a reduced current capability
at pins SO*.
The test voltage of 4000 Vac(rms)/50 Hz may be applied only once during one minute. It should
be noted that with this (strictly speaking obsolete) test method, some (minor) damage occurs to
the insulation layers due to the partial discharge. Consequently, this test is not performed at
CONCEPT as a series test. Where repeated insulation tests (e.g. module test, equipment test,
system test) are run, the subsequent tests should be performed at a lower test voltage: the test
voltage is reduced by 400 V for each additional test. The more modern if more elaborate partial-
discharge measurement is preferable to such test methods as it is almost entirely non-destructive.
The partial discharge test is performed for each driver within the scope of series production.
The supported gate charge refers to the stability of the power supply voltages and to a dynamic
voltage drop of 0.3V. Exceeding the maximum supported gate charge may lead to malfunction or
thermal overload of the gate drivers. The customer may increase the specified maximum value of
the supported gate charge by connecting additional supply capacitors between terminals Cs and
COM up to a total of 47μF. Absolute gate charge must not exceed 55μC.
between
any
primary-side
pin
IHD260/660
and
Preliminary Data Sheet
any
secondary-side
Page 11
pin.