AN1526 Freescale Semiconductor / Motorola, AN1526 Datasheet - Page 2
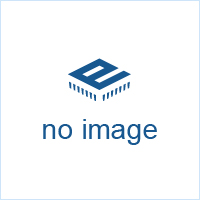
AN1526
Manufacturer Part Number
AN1526
Description
RF Power Device Impedances: Practical Considerations
Manufacturer
Freescale Semiconductor / Motorola
Datasheet
1.AN1526.pdf
(16 pages)
input reflection coefficient magnitudes very close to one,
requiring drive levels far beyond the capability of a standard
network analyzer to merely turn the device on, if operated
in class–C. This restriction can be alleviated to some extent,
by providing a degree of impedance matching between the
network analyzer ports and the device, and de–embedding
the device from the impedance transforming network. There
is also a question of the validity of the S22 and S12
measurements for class–C design. If the device is biased
off, as is normally the case in class–C, the measurements
of these two parameters will be in err. Ideally, the transistor
should be operating with drive applied to the input when
making these measurements. The test signal can then be
applied to the output port and the reverse gain and output
reflection coefficient measured with the device at a normal
operating bias. This method is described in more detail by
Mazumder [8]. Harmonic loading of the device is a factor
not addressed by most large–signal s–parameter proponents
but plays a significant part in the non–linear operation of RF
power amplifiers.
caution. Making a direct connection of a network analyzer
to a potentially unstable 100
hazardous to the network analyzer. Custom built test sets
and measurement systems are almost always required.
Further, this type of characterization gives the designer no
information as to how other parameters, such as efficiency,
behave with fundamental load impedance variations.
Load–Pull
literature as “load–pull” [16]–[24]. This technique results in
the graphical presentation of a performance parameter such
as gain, efficiency or IMD, versus a source or load
impedance. Although the technique has been known for
some time, the widespread availability of desktop computers
and automatic tuning systems is just now making this method
more attractive, particularly for higher power devices. The
characterization process is conceptually quite simple. A
variety of load impedances are presented to the device as
shown in Figure 16. The performance of the device is
measured at each one of these points, and fed into a surface
generating program. (See the appendix for further
information). Figure 1 shows an example of how the gain
of the 15 watt MRF873 varies at 870 MHz with various
fundamental frequency load impedances. Figure 2 shows
how the collector efficiency of this device varies under the
same conditions. The influence of output load impedance
on input impedance, due to finite reverse transfer, is
illustrated by the input return loss surface in Figure 3. These
surface plots are converted to contour plots in Figures 4–15.
Now the designer can easily see areas of the reflection
coefficient plane where the matching network should not be
centered, due to a high degree of variability in a particular
performance parameter. A method has been proposed by
Stancliff and Poulin [25] to examine the load–pull
performance of a device by varying not only the fundamental
frequency impedance presented to the device, but also the
second harmonic impedance as well. This technique can
provide the designer with extremely useful information about
the device’s behavior.
2
Devices with output power ratings above a few watts have
In addition, these measurements require EXTREME
Another characterization technique is referred to in the
+
watt device could be very
Freescale Semiconductor, Inc.
For More Information On This Product,
Go to: www.freescale.com
MOTOROLA SEMICONDUCTOR APPLICATION INFORMATION
general, load–pull data is usable only at the operating
conditions at which it is measured. As can be seen in Figure
16, a large set of load impedance points must be presented
to the device output, in order to construct the power gain
and efficiency contours. Changes in bias voltage or output
power require the re–taking of data over the same range
of load impedance conditions. Without proper equipment this
type of characterization is very tedious, time consuming, and
prone to errors. With the advent of automated tuners
measurement of the data is not as time intensive as some
of the earlier methods, and computer software can be used
to manipulate the data and fit the contours. For power
devices it does require a test fixture with some degree of
impedance matching, and the matching networks must be
characterized so that the device impedances can be
de–embedded.
with frequency can be optimized for flatness and best
efficiency, by selecting a low frequency load line impedance
on a constant gain circle that compensates for the inherently
higher gain of the transistor at lower frequency. Broadband
solutions from network design programs i.e. SuperCompact
and Touchstone can be evaluated to assess how much they
have comprised gain and efficiency throughout the band in
arriving at a broadband match.
Large–Signal Series Equivalent Impedances
used by Motorola is that of large–signal series equivalent input
and output impedances as presented by Hejhall [13]. Almost
every RF power device in Motorola’s RF Device Data Book
has a section identifying the device’s large–signal series
equivalent input and output impedances. Most often, the
device output impedance is referred to as “the complex
conjugate of the optimum load impedance into which the
device output operates at a given output power, voltage and
frequency.” That is certainly a statement requiring some
careful thought, especially since the term “output impedance”
is somewhat misleading. The designer new to high power
devices should be aware that this so called “output
impedance” has no connection with the S
measurement. Rather, as described in [13], it is the conjugate
of the LOAD impedance at the fundamental operating
frequency which allowed the transistor to “function properly.”
The designer should also be aware that the characterizations
on a device’s data sheet are valid for some very specific
conditions of frequency, supply voltage, input or output
power, bias levels, harmonic loading and even flange
temperature. The output impedance published in the data
sheet is usually the conjugate of the LOAD impedance that
provides maximum gain at a given output power. Suppose
the designer is interested in maximum efficiency, not
maximum gain. As seen in the load–pull contours the
fundamental frequency load impedance producing maximum
efficiency does not coincide with the maximum gain
impedance. It is up to the device designer to choose which
impedance gets published. One is just as valid as the other.
However, quite frankly, gain is what sells devices. Likewise,
Figures 7, 11 and 15 show how the input return loss, and
thus the device input impedance, is also a function of the
load impedance. The input impedance for higher power
These benefits do not come without some labor. In
If data is available over the whole band, the gain response
The classic technique of high power device characterization
22
small–signal