A3952SW ALLEGRO [Allegro MicroSystems], A3952SW Datasheet - Page 6
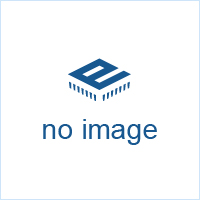
A3952SW
Manufacturer Part Number
A3952SW
Description
FULL-BRIDGE PWM MOTOR DRIVER
Manufacturer
ALLEGRO [Allegro MicroSystems]
Datasheet
1.A3952SW.pdf
(16 pages)
Available stocks
Company
Part Number
Manufacturer
Quantity
Price
Company:
Part Number:
A3952SW
Manufacturer:
ISAHAYA
Quantity:
92
Company:
Part Number:
A3952SW
Manufacturer:
ALLEGRO
Quantity:
14
Company:
Part Number:
A3952SW
Manufacturer:
ALLEGRO
Quantity:
5 510
Part Number:
A3952SW
Manufacturer:
ALLEGRO/雅丽高
Quantity:
20 000
Brake Operation - MODE Input Low
current limit defaults internally to a value approximated by
In this mode, the value of R
independent of V
differing run and brake currents and no practical method of
varying V
current limiting during braking. Therefore, care should be
taken to ensure that the motor’s current does not exceed
the absolute maximum ratings of the device. The braking
current can be measured by using an oscilloscope with a
current probe connected to one of the motor’s leads.
RC Fixed OFF Time
shot to control the time the driver(s) remain(s) OFF. The
one shot time, t
selection of an external resistor (R
connected in parallel from the RC terminal to ground. The
fixed OFF time, over a range of values of C
1500 pF and R
tor, the voltage on the RC terminal will begin to decay from
approximately 3 volts. When the voltage on the RC
terminal reaches approximately 1.1 volt, the PWM latch is
set, thereby re-enabling the driver(s).
RC Blanking
PWM control circuit, the C
tor blanking time. This function blanks the output of the
comparator when the outputs are switched by the internal
current control circuitry (or by the PHASE, BRAKE, or
ENABLE inputs). The comparator output is blanked to
prevent false over-current detections due to reverse
recovery currents of the clamp diodes, and/or switching
transients related to distributed capacitance in the load.
time, the comparator’s output is blanked and C
be charged from approximately 1.1 V by an internal current
source of approximately 1 mA. The comparator output
remains blanked until the voltage on C
mately 3.0 volts.
3952
FULL-BRIDGE
PWM MOTOR DRIVER
During braking, with the MODE input low, the peak
Choosing a small value for R
The internal PWM current control circuitry uses a one
When the PWM latch is reset by the current compara-
In addition to determining the fixed OFF-time of the
During internal PWM operation, at the end of the t
REF
.
T
off
= 12 k to 100 k , is approximated by
REF
(fixed OFF time), is determined by the
. This is useful in applications with
I
TRIP
t
off
T
= 1.5 V/R
= R
S
component sets the compara-
determines the I
T
C
S
T
.
T
essentially disables the
) and capacitor (C
S
.
T
reaches approxi-
T
= 820 pF to
TRIP
T
begins to
value
T
off
)
C
time (the crossover delay time is present to prevent
simultaneous conduction of the source and sink drivers).
After the crossover delay, C
current source of approximately 1 mA. The comparator
output remains blanked until the voltage on C
approximately 3.0 volts.
input, C
re-enabled, C
The comparator output remains blanked until the voltage
on C
PWM operation, the minimum recommended value is C
1200 pF 5 %. For all other applications, the minimum
recommended value is C
ensure that the blanking time is sufficient to avoid false
trips of the comparator under normal operating conditions.
For optimal regulation of the load current, the above
values for C
be sized to determine t
load current regulation, see below.
LOAD CURRENT REGULATION WITH THE INTERNAL
PWM CURRENT-CONTROL CIRCUITRY
there is a limit to the lowest level that the PWM current-
control circuitry can regulate load current. The limitation is
the minimum duty cycle, which is a function of the user-
selected value of t
minimum ON-time pulse, t
PWM latch is reset. If the motor is not rotating, as in the
case of a stepper motor in hold/detent mode, or a brush dc
motor when stalled or at startup, the worst-case value of
current regulation can be approximated by
I
where t
load, V
is specified in the electrical characteristics table. When
the motor is rotating, the back EMF generated will influ-
ence the above relationship. For brush dc motor applica-
tions, the current regulation is improved. For stepper
motor applications when the motor is rotating, the effect is
more complex. A discussion of this subject is included in
the section on stepper motors under “Applications”.
115 Northeast Cutoff, Box 15036
Worcester, Massachusetts 01615-0036 (508) 853-5000
(AV)
T
is discharged to near ground during the crossover delay
Similarly, when a transition of the PHASE input occurs,
Similarly, when the device is disabled via the ENABLE
For applications that use the internal fast-decay mode
When the device is operating in slow-decay mode,
T
[(V
reaches approximately 3.0 V.
BB
off
T
BB
is discharged to near ground. When the device is
is the load/motor supply voltage, and t
= R
– V
T
T
SAT(source+sink)
are recommended and the value of R
T
C
is charged by the internal current source.
T
, R
1.05 (t
off
LOAD
and the maxuimum value of the
off
) • t
on(min)
. For more information regarding
is the series resistance of the
T
on(min)
on(min)
= 820 pF 5 %. These values
T
max + t
is charged by an internal
max] – [1.05 (V
, that occurs each time the
off
) • R
LOAD
SAT(sink)
T
reaches
on(min)
+ V
T
D
can
) • t
max
T
off
=
]