A3952SW ALLEGRO [Allegro MicroSystems], A3952SW Datasheet - Page 8
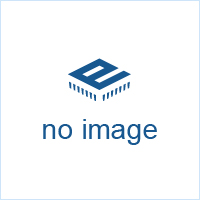
A3952SW
Manufacturer Part Number
A3952SW
Description
FULL-BRIDGE PWM MOTOR DRIVER
Manufacturer
ALLEGRO [Allegro MicroSystems]
Datasheet
1.A3952SW.pdf
(16 pages)
Available stocks
Company
Part Number
Manufacturer
Quantity
Price
Company:
Part Number:
A3952SW
Manufacturer:
ISAHAYA
Quantity:
92
Company:
Part Number:
A3952SW
Manufacturer:
ALLEGRO
Quantity:
14
Company:
Part Number:
A3952SW
Manufacturer:
ALLEGRO
Quantity:
5 510
Part Number:
A3952SW
Manufacturer:
ALLEGRO/雅丽高
Quantity:
20 000
imply that output short circuits are permitted. The hyster-
esis of the thermal shutdown circuit is approximately 15 C.
V
terminal should be connected to ground, and the RC
terminal should be left floating (no connection).
simultaneous conduction of the outputs when the device is
powered up or powered down.
Current Sensing
than the calculated value of I
OFF of the drivers. The amount of overshoot can be
approximated as
where V
back-EMF voltage of the load, R
resistance and inductance of the load respectively, and
t
characteristics table.
tance of 50 k
when determining the impedance of the external circuit
that sets the reference voltage value.
ground trace IR drops, the current-sensing resistor should
have a separate return to the ground terminal of the
device. For low-value sense resistors, the IR drops in the
PCB can be significant and should be taken into account.
The use of sockets should be avoided as their contact
resistance can cause variations in the effective value of
R
but can result in excessive heating and power loss in the
sense resistor. The selected value of R
the SENSE terminal absolute maximum voltage rating to
be exceeded. The recommended value of R
range of
pd(pwm)
REF
S
3952
FULL-BRIDGE
PWM MOTOR DRIVER
.
If the internal current-control circuitry is not used; the
An internal under-voltage lockout circuit prevents
The actual peak load current (I
The reference terminal has an equivalent input resis-
To minimize current-sensing inaccuracies caused by
Larger values of R
terminal should be connected to V
I
is the propagation delay as specified in the electrical
OUTP
BB
is the load/motor supply voltage, V
(V
BB
R
30%. This should be taken into account
S
– [(I
= (0.375 to 1.125)/I
TRIP
S
reduce the aforementioned effects
• R
TRIP
LOAD
L
LOAD
LOAD
due to delays in the turn
) + V
OUTP
and L
BEMF
TRIP
) will be greater
CC
S
must not cause
, the SENSE
.
]) • t
LOAD
S
BEMF
is in the
pd(pwm)
are the
is the
ground allowing the device to be used in microstepping,
sinusoidal, and other varying current profile applications.
Thermal Considerations
maximum junction temperature be kept as low as possible,
typically 90 C to 125 C. The junction temperature can be
measured by attaching a thermocouple to the power tab/
batwing of the device and measuring the tab temperature,
T
using the formula
where V
determined from the electrical specification table for the
given level of I
package thermal resistance table for the appropriate
package.
improved by 20 to 30% by adding a section of printed circuit
board copper (typically 6 to 18 square centimeters) con-
nected to the batwing terminals of the device.
currents and/or high duty cycles can be improved by adding
external diodes in parallel with the internal diodes. In
internal PWM slow-decay applications, only the two top-side
(flyback) diodes need be added. For internal fast-decay
PWM, or external PHASE or ENABLE input PWM applica-
tions, all four external diodes should be added for maximum
junction temperature reduction.
115 Northeast Cutoff, Box 15036
Worcester, Massachusetts 01615-0036 (508) 853-5000
T
. The junction temperature can then be approximated by
The current-sensing comparator functions down to
For reliable operation, it is recommended that the
The power dissipation of the batwing packages can be
The thermal performance in applications with high load
F
is the clamp diode forward voltage and can be
OUT
. The value for R
T
J
T
T
+ (2 V
F
I
OUT
JT
R
is given in the
JT
)