A3952SW ALLEGRO [Allegro MicroSystems], A3952SW Datasheet - Page 7
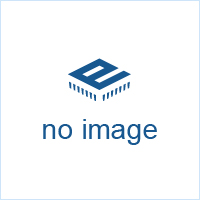
A3952SW
Manufacturer Part Number
A3952SW
Description
FULL-BRIDGE PWM MOTOR DRIVER
Manufacturer
ALLEGRO [Allegro MicroSystems]
Datasheet
1.A3952SW.pdf
(16 pages)
Available stocks
Company
Part Number
Manufacturer
Quantity
Price
Company:
Part Number:
A3952SW
Manufacturer:
ISAHAYA
Quantity:
92
Company:
Part Number:
A3952SW
Manufacturer:
ALLEGRO
Quantity:
14
Company:
Part Number:
A3952SW
Manufacturer:
ALLEGRO
Quantity:
5 510
Part Number:
A3952SW
Manufacturer:
ALLEGRO/雅丽高
Quantity:
20 000
worst-case slow-decay internal PWM load current regula-
tion in the system:
Set V
current control operating in slow-decay mode, use an
oscilloscope to measure the time the output is low (sink
ON) for the output that is chopping. This is the typical
minimum ON time (t
should be increased until the measured value of t
equal to t
characteristics table. When the new value of C
set, the value of R
t
equal to 105% of the nominal design value. The worst-
case load current regulation then can be measured in the
system under operating conditions.
internal PWM modes, the performance of the slow-decay
current regulation should be evaluated per the above
procedure and a t
a C
cient blanking during fast-decay internal PWM.
LOAD CURRENT REGULATION WITH EXTERNAL
PWM OF THE PHASE AND ENABLE INPUTS
modulated to regulate load current. Typical propagation
delays from the PHASE and ENABLE inputs to transitions
of the power outputs are specified in the electrical charac-
teristics table. If the internal PWM current control is used,
then the comparator blanking function is active during
phase and enable transitions. This eliminates false
tripping of the over-current comparator caused by switch-
ing transients (see “RC Blanking” above).
E
turns ON and OFF the selected source and sink drivers.
The corresponding pair of flyback and ground clamp
diodes conduct after the drivers are disabled, resulting in
fast current decay. When the device is enabled, the
internal current control circuitry will be active and can be
used to limit the load current in a slow-decay mode.
desire that the internal current limiting circuit function in the
fast-decay mode, the ENABLE input signal should be
inverted and connected to the MODE input. This prevents
the device from being switched into sleep mode when the
ENABLE input is low.
off
NABLE
3952
FULL-BRIDGE
PWM MOTOR DRIVER
= R
T
The following procedure can be used to evaluate the
In applications utilizing both fast- and slow-decay
The PHASE and ENABLE inputs can be pulse-width
With the MODE input low, toggling the ENABLE input
For applications that PWM the ENABLE input, and
value of 1200 pF, which is required to ensure suffi-
REF
T
•C
Pulse-Width Modulation
to 0 volts. With the load connected and the PWM
on(min)
T
(with the artificially increased value of C
max) = 3.0 s as specified in the electrical
on(min)
T
should be decreased so the value for
on(min)
max of 3.8 s. This corresponds to
typ) for the device. C
T
T
then
has been
on(min)
T
) is
is
P
which sink/source pair is enabled, producing a load current
that varies with the duty cycle and remains continuous at
all times. This can have added benefits in bidirectional
brush dc servo motor applications as the transfer function
between the duty cycle on the phase input and the aver-
age voltage applied to the motor is more linear than in the
case of ENABLE PWM control (which produces a discon-
tinuous current at low current levels). See also, “DC Motor
Applications” below.
SYNCHRONOUS FIXED-FREQUENCY PWM
A3952S– devices can be synchronized by using the simple
circuit shown in figure 3. A 555 IC can be used to gener-
ate the reset pulse/blanking signal (t
the PWM cycle (t
of 1.5 s in slow-decay mode and 2 s in fast-decay
mode. When used in this configuration, the R
components should be omitted. The PHASE and ENABLE
inputs should not be PWMed with this circuit configuration
due to the absence of a blanking function synchronous
with their transitions.
terminals puts the device into a sleep mode to minimize
current consumption when not in use.
currents that can occur when switching phase or braking.
should the junction temperature reach 165 C (typical).
This is intended only to protect the device from failures
due to excessive junction temperatures and should not
Figure 3 — Synchronous Fixed-Frequency Control Circuit
HASE
Toggling the PHASE terminal determines/controls
The internal PWM current-control circuitry of multiple
A logic high applied to both the ENABLE and MODE
An internally generated dead time prevents crossover
Thermal protection circuitry turns OFF all drivers
Pulse-Width Modulation
t
t
2
1
2
). The value of t
2N2222
V
CC
1
should be a minimum
1
) and the period of
1N4001
T
and C
Dwg. EP-060
T
RC
RC
1
N