MAX17006EVKIT+ Maxim Integrated, MAX17006EVKIT+ Datasheet - Page 4
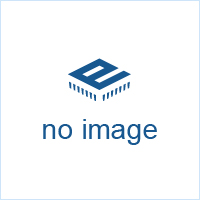
MAX17006EVKIT+
Manufacturer Part Number
MAX17006EVKIT+
Description
Battery Management 1.2MHz Low-Cost High-Performance Chargers
Manufacturer
Maxim Integrated
Series
MAX17005, MAX17006, MAX17015r
Datasheet
1.MAX17006EVKIT.pdf
(10 pages)
Specifications of MAX17006EVKIT+
Operating Supply Voltage
- 0.3 V to + 30 V
Charge Safety Timers
Yes
Operating Supply Current
+/- 1 uA
Product Type
Charge Management
Temperature Monitoring
No
Uvlo Start Threshold
7.9 V
Uvlo Stop Threshold
8.9 V
MAX17006 Evaluation Kit
2- or 3-cell charging operation. Jumper JU2 sets the
battery-charge-voltage threshold to 4.2V or 4.35V per
cell. The charge current can be configured from 0.14A
to 4A by adjusting the analog DC voltage at the ISET
test point connector using potentiometer R9, or by
applying a PWM signal at ISET. The EV kit also features
an ACOK output test point to monitor the presence of a
valid input source connected at ADAPTER. See the
Setting Charge Current section for additional informa-
tion when using a PWM signal at ISET.
To provide power at SYS_LOAD, the MAX17006 EV kit
requires a 10V to 25V power source connected to the
ADAPTER and PGND test points, or a power source
with a 6V to 13.05V output-voltage range connected to
the BATT+ and BATT- test points.
In a typical battery-charging application, the battery
pack is connected between the BATT+ and BATT-
terminals and an AC adapter power supply is connect-
ed between the ADAPTER and PGND terminals. When
the voltage at the MAX17006 DCIN pin is greater than
BATT+ by 420mV, the MAX17006 BST output drives the
gates of n-channel MOSFETs N1 and Q1-A approxi-
mately 4.5V above the ADAPTER voltage, selecting
ADAPTER as the main power source for supplying the
load at SYS_LOAD. As long as the ADAPTER power
source is present, though the charger is off, there are
forced BST refresh pulses at a 5ms (min) period at the
MAX17006 BST pin to properly conduct the system-
load current through N1 and Q1-A.
The MAX17006 EV kit charges the batteries connected
between the BATT+ and BATT- terminals when the fol-
lowing conditions are met:
1) ADAPTER > (BATT+) + 420mV (300mV falling
2) SYS_LOAD current is less than the input-current limit.
3) Jumper JU3 is not installed and a DC analog volt-
When the ADAPTER power source is removed, the
MAX17006 stops generating BST refresh pulses and
N2 forces N1 off. BATT+ is then selected as the
SYS_LOAD power source by conducting the system-
load current through the p-channel MOSFET, Q1-B.
4
Power-Source Selection for System Load
hysteresis).
age > 26mV or a PWM signal is present at the ISET
test point.
_______________________________________________________________________________________
The EV kit features the ACOK output-logic signal that
indicates the presence of a valid source connected to
the ADAPTER terminal. ACOK is pulled low when the
voltage at ADAPTER is > 20V; otherwise, ACOK is pulled
to the MAX17006 reference output voltage V
The EV kit input-source current limit is set at 4A using
resistor R1. The input current is the sum of the system-
load current and battery-charge current when the
ADAPTER input is the main power source. When the
input current exceeds the input-current limit, the charg-
ing current is reduced to provide priority to the
SYS_LOAD current. As the SYS_LOAD current
approaches the current-limit threshold, the charge cur-
rent drops linearly to zero.
The maximum input-source current limit can be set by
replacing sense resistor R1. Use the following equation
to select a new sense-resistor value:
where I
and R1 is the value of the sense resistor in milliohms.
Refer to the Setting Input-Current Limit section in the
MAX17005/MAX17006/MAX17015 IC data sheet for
additional information on setting the input-current limit if
populating resistors at the R2 and R3 PCB pads.
The MAX17006 EV kit supports 2- or 3-cell Li+ battery
charging. Jumper JU1 configures the MAX17006 for
2- or 3-series-cell charging operation. Remove the shunt
at jumper JU1 for 3-cell charging operation. Install a
shunt at jumper JU1 for 2-cell charging operation.
See Table 1 for proper jumper JU1 configuration.
Table 1. Charge Cell Count (Jumper JU1)
Not installed
POSITION
Installed
SHUNT
LIMIT
is the input-source current limit in amperes
R m
1
ACOK Output Logic Signal
(
Ω =
)
NUMBER OF SERIES
Battery Cell-Count Setting
CELLS CHARGED
60
I
LIMIT
Input-Current Limit
mV
Battery Charging
3
2
AA
(4.2V).