MAX17006EVKIT+ Maxim Integrated, MAX17006EVKIT+ Datasheet - Page 5
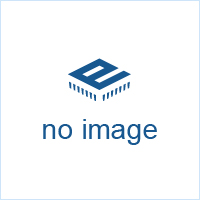
MAX17006EVKIT+
Manufacturer Part Number
MAX17006EVKIT+
Description
Battery Management 1.2MHz Low-Cost High-Performance Chargers
Manufacturer
Maxim Integrated
Series
MAX17005, MAX17006, MAX17015r
Datasheet
1.MAX17006EVKIT.pdf
(10 pages)
Specifications of MAX17006EVKIT+
Operating Supply Voltage
- 0.3 V to + 30 V
Charge Safety Timers
Yes
Operating Supply Current
+/- 1 uA
Product Type
Charge Management
Temperature Monitoring
No
Uvlo Start Threshold
7.9 V
Uvlo Stop Threshold
8.9 V
The EV kit’s battery-charge voltage can be configured
between 4.2V to 4.4V per cell for the MAX17006 using
on-board circuitry resistor R12 and U2. Jumper JU2
sets the EV kit’s battery-cell voltage to 4.2V or 4.35V.
Install the shunt at jumper JU2 to set the EV kit battery-
cell voltage to 4.2V. Remove the shunt at jumper JU2 to
set the battery-cell voltage to 4.35V.
See Table 2 for proper jumper JU2 configuration when
setting the battery cell voltage.
The MAX17006 battery-cell voltage can be configured
from 4.2V/cell to 4.4V/cell by replacing resistor R12,
which adjusts the voltage at the VCTL pin.
Use the following equations to first calculate the VCTL
voltage for the desired cell voltage:
1) For 3-cell selection, 4.2V > V
OR
2) For 2-cell selection of MAX17006, 0V < V
Using the V
1 and 2, use the respective equations below to calcu-
late the total high- or low-side resistance (RT) needed
at the VCTL parallel-resistor network, where RT is R11||
R12 or R14||R12:
3) For 3-cell selection of MAX17006:
Table 2. Battery-Voltage Cell Charge
(Jumper JU2)
Not installed
POSITIONS
1.8V.
Installed
SHUNT
VCTL
V
V
RT
VCTL
VCTL
voltage calculated above in equations
_______________________________________________________________________________________
=
4.35V/cell or adjusted battery-cell voltage
RT
150
=
= ×
=
29 4
6
k
Ω
⎛
⎝ ⎜
.
V
BATTERY-VOLTAGE/
V
×
4 2
VCTL
V
150
CELL
.
CELL OPERATION
⎛
⎜
⎝
V
−
V
4 2
Setting Charge Voltage
VCTL
k
.
6
Ω
VCTL
4.2V/cell
−
−
×
V
1
V
25 2 .
⎞
⎠ ⎟
CELL
−
> 2.4V.
1
⎞
⎟
⎠
V
VCTL
<
MAX17006 Evaluation Kit
4) For 2-cell selection of MAX17006.
Upon calculating RT, and using the EV kit’s R11 or R14
default 150kΩ value, determine the new R12 resistor
value.
The total BATT+ to BATT- battery regulation voltage
can be calculated using the following equation:
where V
is the total number of cells, and V
age setting.
The MAX17006 EV kit charge current can be set up to
3.5A or 3A when applying an analog DC voltage or
PWM signal, respectively, at the ISET terminal.
Potentiometer R9 adjusts the battery-charge current by
applying the proper analog DC voltage at the ISET pin.
While monitoring the ISET voltage through the EV kit’s
ISET test point, use the following equation to adjust the
maximum battery-charge current to the desired value:
where V
the 20mΩ battery current-sense resistor, and I
is the desired battery-charge current.
A digital PWM signal with a 128Hz to 500kHz frequency
range can be applied at the ISET terminal to control
the battery charging current. Refer to the Setting
Charge Current section in the MAX17005/MAX17006/
MAX17015 IC data sheet for proper logic levels and
charge-current setting when using a PWM signal at
ISET. As the duty cycle increases/decreases, the
charge current linearly increases/decreases.
The EV kit’s actual battery-charge current depends on the
input-source-current limit and the load connected at
SYS_LOAD. As the battery and SYS_LOAD current
exceeds the input-source current limit, the charging current
is reduced to provide priority to the SYS_LOAD current.
BATT+
ISET
is the voltage at the ISET test point, R16 is
V
is the battery regulation voltage, N
ISET
V
BATT
≅
+
I
CHARGE
=
N
CELLS
0 24
.
×
Setting Charge Current
R
×
16 4 2
V
CELL
CELL
×
.
is the cell volt-
CHARGE
CELLS
5