XRP7724EVB-DEMO-2P-KIT Exar, XRP7724EVB-DEMO-2P-KIT Datasheet - Page 25
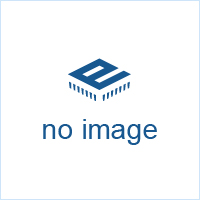
XRP7724EVB-DEMO-2P-KIT
Manufacturer Part Number
XRP7724EVB-DEMO-2P-KIT
Description
Power Management IC Development Tools Eval Kit for XRP7724
Manufacturer
Exar
Type
PWM Controllersr
Datasheet
1.XRA1402IG16-F.pdf
(26 pages)
Specifications of XRP7724EVB-DEMO-2P-KIT
Product
Demonstration Kits
Tool Is For Evaluation Of
XRP7724
Input Voltage
4.75 V to 25 V
Output Voltage
0.6 V to 5.5 V
Interface Type
I2C
Maximum Operating Temperature
+ 125 C
Minimum Operating Temperature
- 40 C
Output Current
130 mA
For Use With
XRP7724
8.5 Improvement
8.5.1 Continual Improvement
8.5.2 Corrective Action
8.5.3 Preventive Action
Strategic objectives, established as an integral part of the annual business plan, define the expected
results from the Company’s processes. A key overall objective is Customer satisfaction, which begins
with a thorough understanding of Customer requirements. Improvements in Customer satisfaction are
achieved through the quality management system processes defined on Figure 2. Also shown on
Figure 2 are the measurements used to provide feedback to the processes in order to continually
improve effectiveness and ultimately to improve Customer satisfaction, done through the use of the
quality policy, quality objectives, audit results, analysis of data, corrective and preventive actions and
Executive Management Team review.
The corrective action system eliminates causes of non-conforming product and system deficiencies,
by identifying root cause and implementing corrective action plans to avoid reoccurrence.
Corrective Action Request coordinator evaluates discrepant material reports issued to Manufacturing
and initiates Corrective Action Requests when warranted. Corrective Action Requests are issued to
subcontractors when appropriate.
Marketing and/or Sales records nonconformities of product at the customer. Necessary information is
transmitted to the Director, Customer Quality Engineering for analysis and corrective action.
For evaluation and traceability purposes the corrective action report is generated per requested format
as defined in the applicable specification. Records of the results of action taken shall be maintained.
Results of corrective actions are reported to the Executive Management Team for review.
Available trend data from quality monitoring and process performance in addition to corrective action
results, Customer complaints, failure analysis results, audit observation, etc. form the basis of
preventive action.
The intent of preventive action is to proactively eliminate potential root causes prior to the occurrence
of non-conformities. The ultimate responsibility of implementing preventive action belongs to not only
each process owner but also the supplying and receiving sides of this process. Evaluation,
qualification, and brainstorming prior to product design or realization are required to discover the
potential deficiencies or problem areas.
Records of preventive action results taken shall be maintained as per applicable specification. The
results of preventive actions are reported to the Executive Management Team for review.
TITLE:
Exar Quality Manual
FOR REFERENCE ONLY
SPEC #: QA031
REV: QQ
PAGE
25 of 26