ADIS16100/PCB Analog Devices Inc, ADIS16100/PCB Datasheet - Page 11
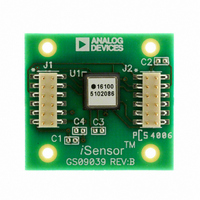
ADIS16100/PCB
Manufacturer Part Number
ADIS16100/PCB
Description
BOARD EVALUATION ADIS16100
Manufacturer
Analog Devices Inc
Series
iSensor™r
Specifications of ADIS16100/PCB
Sensor Type
Gyroscope, 1 Axis
Sensing Range
±300°/sec
Interface
SPI Serial
Voltage - Supply
4.75 V ~ 5.25 V
Embedded
No
Utilized Ic / Part
ADIS16100
Silicon Manufacturer
Analog Devices
Application Sub Type
Angular Rate Sensor / Gyroscope
Kit Application Type
Sensing - Motion / Vibration / Shock
Silicon Core Number
ADIS16100
Kit Contents
Board
Lead Free Status / RoHS Status
Contains lead / RoHS non-compliant
For Use With
ADISUSBZ - KIT EVAL ADIS W/SOFTWARE USBADISEVALZ - KIT PC EVALUATION W/SOFTWARE
Sensitivity
-
Lead Free Status / Rohs Status
Not Compliant
THEORY OF OPERATION
The ADIS16100 operates on the principle of a resonator
gyroscope. Two polysilicon sensing structures each contain a
dither frame that is electrostatically driven to resonance. This
produces the necessary velocity element to produce a Coriolis
force while rotating. At two of the outer extremes of each frame,
orthogonal to the dither motion, are movable fingers that are
placed between fixed pickoff fingers to form a capacitive pickoff
structure that senses Coriolis motion. The resulting signal is fed
to a series of gain and demodulation stages that produce the
electrical rate signal output. The rate signal is then converted to
a digital representation of the output on the SPI pins. The dual-
sensor design rejects external g forces and vibration. Fabricating
the sensor with the signal conditioning electronics preserves
signal integrity in noisy environments.
The electrostatic resonator requires 14 V to 16 V for operation.
Because only 5 V is typically available in most applications, a
charge pump is included on-chip. After the demodulation stage,
there is a single-pole, low-pass filter included on-chip that is
used to limit high frequency artifacts before final amplification.
The frequency response is dominated by the second low-pass
filter, which is set at 40 Hz. For additional bandwidth reduction
options, see the Setting Bandwidth section.
SUPPLY AND COMMON CONSIDERATIONS
Power supply noise and transient behaviors can influence the
accuracy and stability of any sensor-based measurement system.
When considering the power supply for the ADIS16100, it is
important to understand that the ADIS16100 provides 0.2 μF of
decoupling capacitance on the V
of noise present in the system power supply, the ADIS16100
may not require any additional decoupling capacitance for this
supply. The analog supply, V
V
in receiving the digital output data. V
downstream logic power supply and supports standard 3.3 V
and 5 V logic families. The V
decoupling capacitors.
INCREASING MEASUREMENT RANGE
The full-scale measurement range of the ADIS16100 is increased
by placing an external resistor between the RATE pin and FILT
pin, which results in a parallel connection with the internal
180 kΩ, 1% resistor. For example, a 330 kΩ external resistor
gives ~50% increase in the full-scale range. This is effective for
up to a 4× increase in the full-scale range (minimum value of
the parallel resistor allowed is 45 kΩ). The internal circuitry
headroom requirements prevent further increase in the linear
full-scale output range. The trade-offs associated with increasing
the full-scale range are potential increase in output null drift (as
much as 2°/sec over temperature) and introducing initial null
bias errors that must be calibrated.
DRIVE
, are segmented to allow multiple logic levels to be used
CC
DRIVE
, and the digital interface supply,
CC
supply does not have internal
pin. Depending on the level
DRIVE
is intended for the
Rev. D | Page 11 of 16
SETTING BANDWIDTH
An external capacitor can be used in combination with an
on-chip resistor to create a low-pass filter to limit the bandwidth
of the ADIS16100 rate response.
The −3 dB frequency is defined as
where:
R
manufacturing to 180 kΩ ± 1%.
C
Any external resistor applied between RATE and FILT results in
where R
With C
is obtained based upon an internal 0.022 μF capacitor implemented
on-chip.
SELF-TEST FUNCTION
The ADIS16100 includes a self-test feature that actuates each of
the sensing structures and associated electronics in the same
manner as if subjected to an angular rate. It provides a simple
method for exercising the mechanical structure of the sensor,
along with the entire signal processing circuit. It is activated by
standard logic high levels applied to Input ST1, Input ST2, or
both. ST1 causes a change in the digital output equivalent to
typically −221 LSB, and ST2 causes an opposite +221 LSB change.
The self-test response follows the viscosity temperature dependence
of the package atmosphere, approximately 0.25%/°C. Activating
both ST1 and ST2 simultaneously is not damaging. Because
ST1 and ST2 are not necessarily closely matched, actuating both
simultaneously can result in an apparent null bias shift.
Continuous Self-Test
As an additional failure detection measure, a power-on self-test can
be performed. However, some applications warrant a continuous
self-test while sensing rate.
RATE SENSITIVE AXIS
OUT
OUT
LONGITUDINAL
is the internal impedance that was trimmed during
is the external capacitance across the RATE and FILT pins.
R
f
OUT
OUT
OUT
AXIS
EXT
Figure 20. Rate Signal Increases with Clockwise Rotation
=
=
= 0 μF, a default −3 dB frequency response of 40 Hz
1
is the external resistor.
1/
(
LATERAL
180
(
AXIS
2
RATE
AXIS
× ×
kΩ
π
4 5
×
R
R
OUT
8
EXT
×
) (
(
/
C
180
OUT
RATEOUT
kΩ
+
0.022
+
R
EXT
μF
)
))
ADIS16100
+2047 LSB
–2048 LSB
CLOCK-WISE
ROTATION