MAX8538EEI+ Maxim Integrated Products, MAX8538EEI+ Datasheet - Page 15
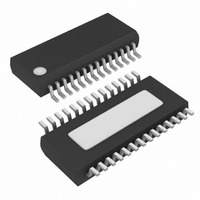
MAX8538EEI+
Manufacturer Part Number
MAX8538EEI+
Description
IC CNTRLR BUCK DUAL 28-QSOP
Manufacturer
Maxim Integrated Products
Datasheet
1.MAX8538EEI.pdf
(23 pages)
Specifications of MAX8538EEI+
Applications
Controller, DDR
Voltage - Input
4.5 ~ 23 V
Number Of Outputs
2
Voltage - Output
0.8 ~ 3.6 V
Operating Temperature
0°C ~ 85°C
Mounting Type
Surface Mount
Package / Case
28-QSOP
Output Voltage
0.8 V to 3.6 V
Output Current
30 A
Input Voltage
4.5 V to 23 V
Mounting Style
SMD/SMT
Maximum Operating Temperature
+ 85 C
Minimum Operating Temperature
- 40 C
Case
SSOP
Dc
05+
Lead Free Status / RoHS Status
Lead free / RoHS Compliant
by 10°C, resulting in a pulsed output during continuous
thermal-overload conditions.
During a thermal event, the switching converters are
turned off, POK1 and POK2 are pulled low, and the
soft-starts are reset.
The output voltage can be set by a resistive divider net-
work. Select R2, the resistor from FB to GND, between
5kΩ and 15kΩ. Then calculate R1 by:
There are several parameters that must be examined
when determining which inductor to use: input voltage,
output voltage, load current, switching frequency, and
LIR. LIR is the ratio of inductor current ripple to DC load
current. A higher LIR value allows for a smaller induc-
tor, but results in higher losses and higher output rip-
ple. A good compromise between size and efficiency is
a 30% LIR. Once all the parameters are chosen, the
inductor value is determined as follows:
where f
value close to the calculated value. The exact inductor
value is not critical and can be adjusted in order to
make trade-offs among size, cost, and efficiency.
Lower inductor values minimize size and cost, but also
increase the output ripple and reduce the efficiency
due to higher peak currents. On the other hand, higher
inductor values increase efficiency, but eventually
resistive losses due to extra turns of wire exceed the
benefit gained from lower AC current levels. Find a low-
loss inductor with the lowest possible DC resistance
that fits the allotted dimensions. Ferrite cores are often
the best choice, although powdered iron is inexpensive
and can work well up to 300kHz. The chosen inductor’s
saturation current rating must exceed the peak inductor
current determined as:
The input filter capacitor reduces peak currents drawn
from the power source and reduces noise and voltage
ripple on the input caused by the circuit’s switching.
The input capacitor must meet the ripple current
Load, Tracking, and DDR Memory Power Supplies
Dual-Synchronous Buck Controllers for Point-of-
S
I
PEAK
is the switching frequency. Choose a standard
L
R1 = R2 x [(V
=
=
V
I
IN
LOAD MAX
______________________________________________________________________________________
×
V
OUT
f
(
S
×
Output Voltage Setting
×
Design Procedure
)
I
OUT
(
LOAD MAX
+
V
IN
⎛
⎜
⎝
Inductor Selection
LIR
/ 0.8) -1]
2
−
(
⎞
⎟ ×
⎠
Input Capacitor
V
OUT
)
I
×
LOAD MAX
)
LIR
(
)
requirement (I
defined by the following equation:
Combinations of large electrolytic and small ceramic
capacitors in parallel are recommended. Almost all of
the RMS current is supplied from the large electrolytic
capacitor, while the smaller ceramic capacitor supplies
the fast rise and fall switching edges. Choose the elec-
trolytic capacitor that exhibits less than 10°C tempera-
ture rise at the maximum operating RMS current for
optimum long-term reliability.
The key selection parameters for the output capacitor
are the actual capacitance value, the equivalent series
resistance (ESR), the equivalent series inductance
(ESL), and the voltage-rating requirements, which
affect the overall stability, output ripple voltage, and
transient response.
The output ripple has three components: variations in
the charge stored in the output capacitor, voltage drop
across the capacitor’s ESR, and voltage drop across
the capacitor’s ESL, caused by the current into and out
of the capacitor. The following equations estimate the
worst-case ripple:
where I
Inductor Selection section). Higher output current
requires paralleling multiple capacitors to meet the out-
put ripple voltage.
The MAX8537/MAX8538/MAX8539s’ response to a load
transient depends on the selected output capacitor.
After a load transient, the output instantly changes by
(ESR x ∆I
can respond, the output deviates further depending on
the inductor and output capacitor values. After a short
period of time (see the Typical Operating Characteris-
tics), the controller responds by regulating the output
voltage back to its nominal state. The controller
response time depends on the closed-loop bandwidth.
With higher bandwidth, the response time is faster, pre-
I
RMS
V
RIPPLE
=
P-P
[
V
I
OUT
RIPPLE C
V
=
LOAD
RIPPLE ESL
is the peak-to-peak inductor current (see the
1
2
V
×
I
RIPPLE ESR
P P
RMS
V
V
OUT
−
( )
) + (ESL x dI/dt). Before the controller
RIPPLE ESR
(
1
=
) imposed by the switching currents
=
×
⎛
⎜
⎝
(
(
V
)
I
V
IN
P P
(
=
IN
−
−
f
V
SW
V
)
−
IN
OUT
+
)
/ (
V
V
=
OUT
1
×
8
L
RIPPLE C
)] [
V
+
IN
I
P P
ESL
×
I
−
OUT
⎞
⎟
⎠
⎛
⎜
⎝
Output Capacitor
C
V
ESR
2
( )
OUT
/ (
2
OUT
V
IN
×
L
V
+
OUT
+
V
⎞
⎟
⎠
×
RIPPLE ESL
2
ESL
×
f
SW
(
V
IN
)
)
−
(
V
OUT
)
2
)]
15