MCIMX286CVM4B Freescale Semiconductor, MCIMX286CVM4B Datasheet - Page 4
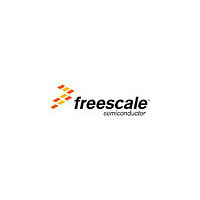
MCIMX286CVM4B
Manufacturer Part Number
MCIMX286CVM4B
Description
IC MPU I.MX286 289MAPBGA
Manufacturer
Freescale Semiconductor
Series
i.MX28r
Datasheets
1.MCIMX283DVM4B.pdf
(70 pages)
2.MCIMX283DVM4B.pdf
(2 pages)
3.MCIMX283DVM4B.pdf
(2327 pages)
4.MCIMX283DVM4B.pdf
(20 pages)
Specifications of MCIMX286CVM4B
Core Processor
ARM9
Core Size
32-Bit
Speed
454MHz
Connectivity
CAN, EBI/EMI, Ethernet, I²C, MMC, SmartCard, SPI, SSI, UART/USART, USB OTG
Peripherals
DMA, I²S, LCD, POR, PWM, WDT
Program Memory Size
128KB (32K x 32)
Program Memory Type
Mask ROM
Ram Size
32K x 32
Voltage - Supply (vcc/vdd)
1.25 V ~ 5.25 V
Data Converters
A/D 17x12b
Oscillator Type
External
Operating Temperature
-40°C ~ 85°C
Package / Case
289-LFBGA
Lead Free Status / RoHS Status
Lead free / RoHS Compliant
Number Of I /o
-
Eeprom Size
-
Lead Free Status / Rohs Status
Compliant
PMU and DC-DC Converter
3.2
The DCDC converter switching current loop area should be kept as small as possible to reduce the radiated
emissions. There are two switching current loops as shown below. LOOP1: This occurs during the portion
of the duty cycle when the inductor is being charged. LOOP2: This occurs during the flyback portion of
the duty cycle when the inductor is supplying all of the current to the load.
Minimizing the current loop areas can be accomplished by making sure the following layout rules are
followed:
4
•
•
•
•
•
•
BATTERY
Make sure the DCDC_GND pin has a good low impedance connection to the other i.MX28 ground
pins. If a voltage difference is created between the DCDC_GND pin and the other i.MX28 VSS
pins, the system may be more susceptible to ESD failure.
The power inductor traces should be 15-20 mils thick and should not use vias. If for some reason
the power inductor cannot be placed on the same side of the PCB as the i.MX28, then multiple vias
should be used to connect the inductor to the i.MX28 DC-DC converter pins.
All vias used for the i.MX28 PMU power (VDD) and ground (VSS) pins, including the
DCDC_GND pin, should have a drill hole size of 8 mils or larger to ensure a low
impedance/inductive path between the pin and the PCB power/ground plane.
Place the DCDC_BATT pin input capacitors as close as possible to the DCDC_BATT pin (less than
5mm away).
Place the DCDC inductor as close as possible to the DCDC_LP and DCDC_LN pins.
Route the inductor traces close together.
Minimize Switching Current Loops
LOOP1
Current loop during
inductor charging.
DCDC_GND
DCDC_BATT
VDDIO
i.MX28 Layout and Design Guidelines, Rev. 0
i.MX
BATTERY
LOOP2
DCDC_GND
DCDC_BATT
Current loop during
inductor discharge.
VDDIO
Freescale Semiconductor
i.MX