TMC222-SI TRINAMIC, TMC222-SI Datasheet - Page 40
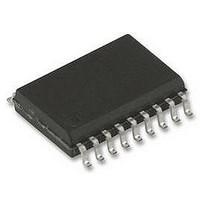
TMC222-SI
Manufacturer Part Number
TMC222-SI
Description
IC, MOTOR CTRL/DRVR, STEPPER, SOIC-20
Manufacturer
TRINAMIC
Datasheet
1.TMC222-SI.pdf
(47 pages)
Specifications of TMC222-SI
Motor Type
Stepper
No. Of Outputs
4
Output Current
800mA
Supply Voltage Range
8V To 29V
Driver Case Style
SOIC
No. Of Pins
20
Operating Temperature Range
-40°C To +125°C
Device Type
Motor
Lead Free Status / RoHS Status
Lead free / RoHS Compliant
Available stocks
Company
Part Number
Manufacturer
Quantity
Price
Part Number:
TMC222-SI
Manufacturer:
TRINAMI
Quantity:
20 000
40
TMC222 DATASHEET (V. 1.06 / March 15, 2007)
7.4 Finding the reference position
Q: How do I find a reference position?
A: The recommended way is to use the RunInit command. Two motions are specified through RunInit.
The first motion is to reach the mechanical stop. Its target position should be specified far away
enough so that the mechanical stop will be reached from any possible starting position. There is no
internal stall detection so that at the end of the first motion the step motor will bounce against the
mechanical stop loosing steps until the internal target position is reached. The second motion then
can be used either to drive in the opposite direction out of the mechanical stop right into the reference
position which is a known number of steps away from the mechanical stop. Or the second motion can
slowly drive a few steps in the same direction against the mechanical stop to compensate for the
bouncing of the faster first motion and stop as close to the mechanical stop as possible.
Q: Can the SWI input help in finding a reference position?
Not directly. The current state of the SWI input is reflected by the ESW flag which can only be polled
using the command GetFullStatus1. The SWI input resp. the ESW flag have neither influence on any
internal state machine nor on command processing. The recommended way to find a reference
position is to use the RunInit command. Alternatively one could initiate a long distance motion at very
low speed using SetPosition and then poll ESW as frequently as possible to be able to stop the
motion using HardStop right in the moment the switch position is reached. Then one would reset the
internal position counters ActPos and TagPos using the ResetPosition command.
Q: What is the logic of the ESW flag?
A: The ESW flag reflects the state of the SWI input. ESW is set to one if SWI is high or low, i.e.
pulled to VBAT or to GND. ESW is set to zero if SWI is left open, i.e. floating. ESW is updated
synchronously with ActPos every 1024 µs.
Q: Is it possible to swap the logic of the ESW flag?
A: No, it’s not. Actually this is not necessary since the ESW flag must be polled and evaluated by
software anyway. The state of ESW has neither effect on any internal state machine nor on command
processing.
Q: What else is important for the RunInit command?
A: The first target position of RunInit must be different from the current position before sending
RunInit and the second target position must be different from the first one. Otherwise a deadlock
situation can occur. During execution of RunInit only Get… commands should be sent to the device.
Q: Does the second motion of RunInit stop when the ESW flag changes, or does it continue
into the mechanical stop?
A: Neither nor. The SWI input resp. the ESW flag have neither effect on any internal state machine
nor on command processing, i.e. the RunInit command is not influenced by SWI / ESW. The same is
true for the mechanical stop: as there isn’t any internal stall detection the RunInit command can not
detect a mechanical stop. When the mechanical stop is hit the first or second motion of RunInit (or
the motion of any other motion command) will be continued until the internal position counter ActPos
has reached the target position of this motion. This results in the motor bouncing against the
mechanical stop and loosing steps. The intention of the second motion of RunInit is to drive out of the
mechanical stop (reached by the first motion) to the desired reference position at a known distance
from the mechanical stop or to drive slowly against the mechanical stop again to compensate for the
bouncing of the first motion and to come to a standstill as close to the mechanical stop as possible.
Q: Does RunInit reset the position?
A: Yes, it does. After the second motion of RunInit has been finished the internal position counter
ActPos is reset to zero.
Copyright © 2004-2007 TRINAMIC Motion Control GmbH & Co. KG