PGA-016A Littelfuse Inc, PGA-016A Datasheet - Page 48
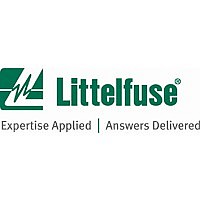
PGA-016A
Manufacturer Part Number
PGA-016A
Description
BULK / WATERTIGHT COVER FOR PGR-6200 / PGR-7200
Manufacturer
Littelfuse Inc
Datasheet
1.PGA-016A.pdf
(64 pages)
Specifications of PGA-016A
Lead Free Status / RoHS Status
Contains lead / RoHS non-compliant
Lead Free Status / RoHS Status
Contains lead / RoHS non-compliant
P
www.littelfuse.com/ProtectionRelays
Selective coordination in a resistance-grounded system can
be achieved if the pick-up setting of each ground-fault relay is
greater than the charging current of the feeder it is protecting.
If the pick-up setting of a ground-fault relay is less than the
charging current of the feeder it is protecting, it will trip when
a ground fault occurs elsewhere in the system. This is known
as sympathetic tripping. If the relative size of the feeders
can change, or if the advantage of using one operating value
for all ground-fault relays in a system is recognized, then it is
prudent to select an pick-up setting for all ground-fault relays
that is larger than the system charging current.
In order to eliminate transient overvoltages associated with
an ungrounded system, it is necessary to use a grounding
resistor with a let-through current equal to or larger than the
system charging current.
What is the minimum acceptable NGR current? Select a
pick-up setting for the ground-fault relays that exceeds the
system charging current and multiply the operating value by
an acceptable tripping ratio. Use the next-largest available
standard let-through current rating.
Motor Protection
Overview
Motors are a significant investment and often run critical
processes. Motor protection relays are used to protect
the windings in the stator from damage due to electrical
faults and thermal overloads. Adequate motor protection
not only prevents motor damage, but also ensures optimal
process efficiency and minimal interruption. Cost recovery
for protection is achieved by extending the life of the motor,
preventing motor rewinds and reducing downtime.
Common Motor Problems
Overload and Overtemperature
Insulation breakdown is a common reason for motor failure.
Windings in the motor are insulated with organic materials
including epoxy and paper. Insulation degradation occurs
when winding temperature exceeds its rating. The National
Electrical Manufacturers Association (NEMA) states that the
time-to-failure of organic insulation is halved for each 8 to
10°C rise above the motor insulation class rating. This point
is illustrated in Figure 11.
Solution: An I
protection of motor windings during all phases of operation. By
integrating the square of the current over time, a thermal model
can predict motor temperature and react much quicker than
embedded temperature devices. A thermal model takes into
consideration the motor service factor, full-load current and class.
A dynamic thermal model adjusts the time-to-trip depending on
how much motor thermal capacity has been used. Figure 12
2
t Thermal Model provides thermal-overload
POWR-GARD
Motor Protection
46
illustrates the adjustment in trip time for different current levels at
different levels of used thermal capacity.
A dynamic thermal model allows conservative protection
of a motor and allows operations to get the maximum
work out of a motor without sacrificing available life. If the
motor is hot (high % used thermal capacity) it will trip more
rapidly during an overload than if the motor is cold (0% used
thermal capacity). In the event of a stall condition, when
available motor torque is lower than the torque required by
the load, the motor can be de-energized before it overheats.
Many old-technology electronic thermal overloads do not
take into consideration the values of load current below
the full-load current (FLA) pick-up value. Modern overload
relays should model currents above and below the FLA pick-
up current to achieve maximum output of the motor and
maximum life of insulation.
On larger induction motors, blockage or loss of ventilation
can cause motor hot spots that current-based protection
cannot detect without the use of temperature sensors.
Resistance temperature detectors (RTDs) are an
inexpensive device installed between the stator windings
during manufacturing and may be included on motor-end
bearings. An RTD has a linear change in resistance over its
rated temperature range. Using information from an RTD,
motor protection relays can provide protection for loss-of-
ventilation, loss-of-cooling, or high-ambient-temperature.
The RTD temperature reading can also be used as input to
the thermal model to improve protection.
When hot-motor compensation is enabled, the maximum
stator-RTD temperature is used to bias the thermal model
by increasing used I
than the thermal-model temperature.
Overcurrent, Jam and Undercurrent
Overcurrent faults, also referred to as short circuits, can
cause catastrophic motor failures and fires. Overcurrents can
be caused by phase-to-phase and phase-to-ground-to-phase
faults.
A mechanical jam, such as a failed bearing or load, can
cause locked-rotor current to be drawn by the motor,
resulting in overheating.
Undercurrent protection is required by some codes as
a safety measure. A water pump that cavitates can be
dangerous. The water typically provides pump cooling.
Without the cooling water, case temperature can reach
an extremely high value. If valves are opened under these
conditions and cold water is allowed to reach red-hot metal
parts, the resulting steam pressures can destroy the pump
and pose a serious personnel hazard.
®
Protection Relays
2
t when the RTD temperature is greater
© 2009 Littelfuse
•
POWR-GARD
®
Protection Relay Catalog