SP7600EB Exar Corporation, SP7600EB Datasheet - Page 8
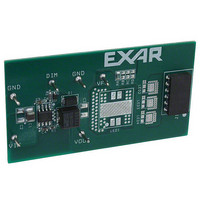
SP7600EB
Manufacturer Part Number
SP7600EB
Description
EVAL BOARD FOR SP7600
Manufacturer
Exar Corporation
Specifications of SP7600EB
Current - Output / Channel
2A
Outputs And Type
1, Non-Isolated
Features
PWM Brightness control
Voltage - Input
4.5 ~ 29 V
Utilized Ic / Part
SP7600
Maximum Operating Temperature
+ 85 C
Minimum Operating Temperature
- 40 C
Product
Display Modules
Core Chip
SP7600
No. Of Outputs
1
Output Current
2A
Output Voltage
200mV
Dimming Control Type
PWM
Development Tool Type
Hardware - Eval/Demo Board
Mcu Supported Families
SP7600
Lead Free Status / RoHS Status
Contains lead / RoHS non-compliant
Voltage - Output
-
Lead Free Status / Rohs Status
Lead free / RoHS Compliant
Other names
1016-1233
THEORY OF OPERATION
The SP7600 is a fixed frequency, Voltage-
mode, non-synchronous buck PWM regulator
optimized for driving LEDs. Constant LED
current is achieved using resistor RFB as
shown in the page 1 schematic. A low 0.2V
reference voltage minimizes power dissipation
in RFB. A tight reference voltage tolerance of
±3%, over full operating conditions, helps
accurately program the LED current. High
switching
reduces the size of passive components.
Dimming and power sequencing is achieved
using a logic-level PWM signal applied to FB
pin via a diode. Overcurrent protection (OCP)
is based on high-side MOSFET’s Rds(on) and is
programmable via a resistor placed at LX
node.
P
Use the following equation to program the LED
current:
The output voltage will adjust as needed to
ensure average I
the output current has to be set at 0.35A then
RFB=0.57 Ohm. If the output LED has a
corresponding Vf of 3.5V then SP7600 will step
down the V
placed in series then SP7600 will step down
the voltage to 7V. Superimposed on I
is a current ripple that is equal in magnitude
to inductor current ripple. Current ripple will
be nominally set to 10% of I
sizing of inductor. Note that throughout this
datasheet
interchangeably.
D
A logic-level PWM signal applied through a
small-signal diode to the feed-back (FB) pin
can be used for dimming control of the LED.
This external signal we call DIM turns the
MOSFET gate drive on/off, thereby modulating
the average current delivered to the LED. The
DIM signal connects to the VFB pin through a
1N4148 diode and will shutdown the SP7600
when DIM = H and turn-on the SP7600 when
© 2009 Exar Corporation
ROGRAMMING THE LED CURRENT
IMMING SIGNAL
IN
frequency
I
Equ.1:
LED
to 3.5V. If two of these LEDs are
LED
and
is supplied. For example if
RFB
of
I
=
O
1.2MHz
0
I
2 .
LED
will
V
LED
by proper
be
2
2
(nominal)
LED
A
A
2
2
there
used
9
9
V
V
N
N
8/13
o
o
n
n
DIM = L. The DIM signal needs to be greater
than 600mV minimum to turn-off the SP7600
and less than 200mV to fully turn-on the
SP7600. It is recommended to use a signal
with DIM = 1V or more for OFF and 0V for ON.
The user should note that the logic is reversed
relative to many other PWM controlled LED
drivers. In other words a logic level high at
20% duty cycle will result in approximately an
80% duty cycle for the LED. Recommended
modulation frequencies are from 100Hz to
200Hz with 10 – 90% duty cycle, 500Hz with
10 – 80% duty cycle, and 1000Hz with 10 -
70% duty cycle. Figures 15 & 16 show the
output response at the maximum PWM DIM
signal of 1000Hz. See figure 17 for 100Hz to
1000Hz duty cycle response for two Luxeon K2
LEDs in parallel at 2A total current.
-
-
S
S
y
y
Fig. 15: 1.1KHz, 10% Duty Cycle Dimming Signal
n
n
c
c
Dimming Signal is ~70% LED Duty Cycle
Dimming Signal is ~10% LED Duty Cycle
.
.
B
B
u
u
Fig. 16: 1KHz, 70% Duty Cycle
c
c
k
k
H
H
i
i
g
g
h
h
P
P
o
o
w
w
e
Ch1: DIM Signal
Ch2: VFB - 2A I
e
r
r
Ch1: DIM Signal
Ch2: VFB - 2A I
L
L
E
E
S
S
D
D
P
P
Rev. 2.0.0
D
D
7
7
r
r
6
6
i
OUT
i
v
v
0
0
OUT
/div
e
e
0
0
r
/div
r