ADNB-6002-EV Avago Technologies US Inc., ADNB-6002-EV Datasheet - Page 6
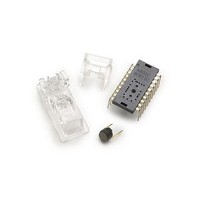
ADNB-6002-EV
Manufacturer Part Number
ADNB-6002-EV
Description
OPT SENS BUNDLE W/A-6000 TL CLIP
Manufacturer
Avago Technologies US Inc.
Specifications of ADNB-6002-EV
Description/function
Laser Mouse Bundle
Interface Type
SPI
Product
Display Modules
Touch Panel
No Touch Panel
For Use With/related Products
ADNS-6000
Lead Free Status / RoHS Status
Lead free / RoHS Compliant
Lead Free Status / RoHS Status
Lead free / RoHS Compliant, Lead free / RoHS Compliant
Notes (for figure 5)
• Caps for pins 11, 12, 16 and 18 MUST have trace lengths LESS than 5
• Pins 16 and 18 caps MUST use pin 17 GND.
• Pin 9, if used, should not be connected to PCB GND to reduce potential
• The 0.1 uF caps must be ceramic.
• Caps should have less than 5 nH of self inductance.
• Caps should have less than 0.2 W ESR.
• NC pins should not be connected to any traces.
• Surface mount parts are recommended.
• Care must be taken when interfacing a 5V microcontroller to the
• VDD3 and GND should have low impedance connections to the
• Because the RBIN pin sets the XY_LASER current, the following PC
• The RBIN resistor should be located close to the sensor pin 13. The
• The pin 13 solder pad and all exposed conductors connected to pin
• The pin 13 solder pad, the traces connected to pin 13, and the RBIN
• The RBIN resistor should be a thru-hole style to increase the distance
LASER Drive Mode
The LASER has 2 modes of operation: DC and Shutter. In
DC mode, the LASER is on at all times the chip is powered
except when in the power down mode via the NPD pin.
In shutter mode the LASER is on only during the portion
of the frame that light is required. The LASER mode is set
by the LASER_MODE bit in the Configuration_bits register.
For optimum product lifetime, Avago Technologies rec-
ommends the default Shutter mode setting (except for
calibration and test).
Laser Bin Table
6
Bin
Number
2A
3A
mm on each side.
RF emissions.
ADNS-6000. Serial port inputs on the sensor should be connected
to open-drain outputs from the microcontroller or use an active
drive level shifter. NPD and RESET should be connected to 5V micro-
controller outputs through a resistor divider or other level shifting
technique.
power supply.
board layout practices should be followed to reduce the chance of
uncontrolled laser drive current caused from a leakage path between
RBIN and ground. One hypothetical source of such a leakage path is
PC board contamination due to a liquid, such as a soft drink, being
deposited on the printed circuit board.
traces between the resistor and the sensor should be short.
13 should be surrounded by a guard trace connected to VDD3 and
devoid of a solder mask.
resistor should be covered with a conformal coating.
between its terminals. This does not apply if a conformal coating is
used.
Rbin Resistor Value
(kohm)
18.7
12.7
Match_Bit
(Reg 0x2C, Bit7)
0
0
Eye Safety
The ADNS-6000 and the associated components in the
schematic of Figure 5 are intended to comply with Class
1 Eye Safety Requirements of IEC 60825-1. Avago Tech-
nologies suggests that manufacturers perform testing to
verify eye safety on each mouse. It is also recommended
to review possible single fault mechanisms beyond those
described below in the section “Single Fault Detection”.
Under normal conditions, the ADNS-6000 generates the
drive current for the laser diode (ADNV-6340). In order to
stay below the Class 1 power requirements, resistor Rbin
must be set at least as high as the value in the bin table of
Figure 5, based on the bin number of the laser diode and
LP_CFG0 and LP_CFG1 must be programmed to appropri-
ate values. Avago Technologies recommends using the
exact Rbin value specified in the bin table to ensure suffi-
cient laser power for navigation. The system comprised of
the ADNS-6000 and ADNV-6340 is designed to maintain
the output beam power within Class 1 requirements
over component manufacturing tolerances and the rec-
ommended temperature range when adjusted per the
procedure below and when implemented as shown in the
recommended application circuit of Figure 5. For more
information, please refer to Avago Technologies Laser
Mouse Eye Safety Calculation Application Note 5088.
LASER Power Adjustment Procedure
1. The ambient temperature should be 25 °C
2. Set VDD3 to its permanent value.
3. Ensure that the laser drive is at 100% duty cycle.
4. Program the LP_CFG0 and LP_CFG1 registers to achieve
Good engineering practices should be used to guarantee
performance, reliability and safety for the product design.
Avago Technologies has additional information and detail,
such as firmware practices, PCB layout suggestions, and
manufacturing procedures and specifications that could
be provided.
an output power as close to 506uW as possible without
exceeding it.
±
5°C.