LM27262 National Semiconductor Corporation, LM27262 Datasheet - Page 17
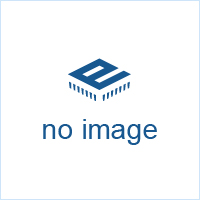
LM27262
Manufacturer Part Number
LM27262
Description
Intel Cpu Core Voltage Regulator Controller For VRD10 Compatible PCS
Manufacturer
National Semiconductor Corporation
Datasheet
1.LM27262.pdf
(22 pages)
Component Selection
Since VRD-10 designs must support large load transients
while maintaining very tight output regulation, a good place
to start the design is the output capacitors.
OUTPUT CAPACITOR SELECTION
For designs that will be subjected to large load current
transients, the output capacitor array is probably the best
place to start. It is assumed that the full amplitude of the load
current step will be drawn from the output capacitors for a
short time. As such, there will be a significant droop in the
output voltage that’s a function of the step size and the
output capacitor’s impedance. The output voltage step will
have three basic components. The first is a more or less
vertical edge equal to the ESR (Equivalent Series Resis-
tance) of the output caps multiplied by the load step ampli-
tude or ∆I x ESR. There’s also a component equal to the ESL
(Equivalent Series Inductance) multiplied by the rate of
change of the load current, (∆I/∆t) x ESL. The ESL induced
spike is usually small in value and short lived, assuming a
clean board layout with good high frequency decoupling, and
can usually be ignored. In sizing the output capacitors, a
good starting point is to assume that the ESR step will be
20% to 50% of the allotted transient voltage spec. The low
end of the range will apply to ceramic capacitors and the
high end of the range to tantalum or aluminum electrolytic
devices. The remainder of the tolerance can be allocated to
the output capacitor’s droop voltage. The droop rate, ∆V/∆t,
is equal to I
load transient. The total droop amplitude is equal to ∆V/∆t
multiplied by the time it takes for the regulator to get the
output voltage slewing in the opposite direction. See Figure
5 for details.
In a design with voltage positioning, the ideal ESR of the
output capacitor array should be less than or equal to the
load line slope. So for a VRD-10 design we should assume
1.5mΩ for the output capacitor ESR.
In a four-phase design, it’s likely that the latency prior to
getting a high-side switch turned on is approximately 1/4 of a
full cycle. An estimate of about twice that, or around 1.5µs, is
a good place to start for making the droop calculation. As an
example, assume a 50 amp load step and a tolerance of
85mV with high performance polymer capacitors: Using a
390µF, 5mΩ capacitor, the design requires a minimum of 4 in
parallel to meet the ESR estimate. The droop in 1.5µs would
be:
Add this to the 75mV ESR droop and we can see the spec is
not met. Therefore several additional capacitors must be
added. Rerunning the numbers with 6 capacitors we get:
Plus an ESR step of 50A x 0.833mΩ + 32mV = 73.6mV
FIGURE 5. Output Transient Response
Droop = 1.5µs x 50A/1560µF = 48mV
Droop = 1.5µs x 50A/2340µF = 32mV
STEP
/C
OUT
, where Istep is the amplitude of the
(Continued)
20083425
17
In general, it will be necessary to add high frequency decou-
pling as well as the bulk capacitance calculated above. An
array of at least 20, 22µF, 1206 case ceramics is recom-
mended. They should be as close to the CPU as possible.
With the output capacitors chosen, an upper bound can be
established for the inductor value:
This value inductor should be installed in each phase. Larger
inductor values will result in a delay in the output voltage
recovery to a load step. Smaller values will store less energy
(lower cost) but will increase the output ripple. Since the
peak switch currents will also be higher, the efficiency is
likely to suffer somewhat with smaller inductors.
Assuming a minimum input voltage of 12V and 1.5V out with
a 50A load step and the capacitors selected above,
Something around 0.5µH will be the closest standard value
and should prove adequate. Since this value is slightly
greater than desired, dynamic performance will suffer
slightly.
If this value will yield excessive ripple current at maximum
input voltage (greater than about 40% of the single phase
DC current), then a larger inductor should be considered and
therefore, optimal dynamic performance will not be obtained.
The tradeoff is typically efficiency vs. dynamic performance.
During a load-off transition, the extra energy stored in the
inductors will end up in the output capacitors. This magnetic
energy, LI
CV
transient, and that left in the inductor after the event, must
also be accounted for.
Therefore:
Where V
phases, I
current, C is the output capacitance, L is the per phase
inductor value, and V
dump.
From our example assuming a 70A max load and a 50A step:
V
2
MAX
FIGURE 6. Normalized Pk-Pk Output Ripple As A
Function Of Duty Factor and Number Of Phases
/2. The energy already in the output capacitor prior to the
V
L
MAX
<
= (4 x 0.50µH x ((70A / 4)
L
MAX
MAX
C
<
2
= [(n x L/C) x ((I
OUT
/2, will be stored in the output capacitors as
2340µF x (12V- 1.5V) x 0.833 mΩ/50A
is the peak output voltage, n is the number of
is the high load current , I
x (V
IN (MIN)
init
L
is the output voltage prior to the load
1.4452)
<
MAX
- V
0.41 µH
OUT(MAX)
/n)
1/2
2
2
–(I
– 20 / 4)
MIN
) x ESR / ∆I
/n)
MIN
2
) + V
2
is the low load
) / 2340µF +
20083426
www.national.com
init
OUT
2
]
1/2