ISL6219 Intersil Corporation, ISL6219 Datasheet - Page 8
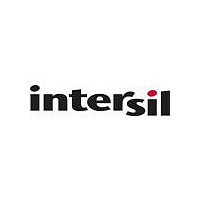
ISL6219
Manufacturer Part Number
ISL6219
Description
Microprocessor CORE Voltage Regulator Precision Multi-Phase BUCK PWM Controller for Mobile Applications
Manufacturer
Intersil Corporation
Datasheet
1.ISL6219.pdf
(17 pages)
Available stocks
Company
Part Number
Manufacturer
Quantity
Price
Company:
Part Number:
ISL6219ACA
Manufacturer:
INTERSIL
Quantity:
200
Company:
Part Number:
ISL6219ACA
Manufacturer:
ALTERA
Quantity:
70
Part Number:
ISL6219ACA
Manufacturer:
INTERSIL
Quantity:
20 000
Part Number:
ISL6219CA
Manufacturer:
INTERSIL
Quantity:
20 000
12V to 1.5V at 36A. The single-phase converter has 11.9A
rms input capacitor current. The single-phase converter
must use an input capacitor bank with twice the rms current
capacity as the equivalent three-phase converter.
Figures 14, 15 and 16 the section entitled can be used to
determine the input-capacitor rms current based on load
current, duty cycle, and the number of channels. They are
provided as aids in determining the optimal input capacitor
solution. Figure 16 shows the single phase input-capacitor
rms current for comparisson.
PWM OPERATION
The number of active channels selected determines the
timing for each channel. By default, the timing mode for the
ISL6219 is 3-phase. The designer can select 2-phase timing
by connecting PWM3 to VCC.
One switching cycle for the ISL6219 is defined as the time
between PWM1 pulse termination signals (the internal signal
that initiates a falling edge on PWM1). The cycle time is the
inverse of the switching frequency selected by the resistor
connected between the FS pin and ground (see Switching
Frequency). Each cycle begins when a clock signal
commands the channel-1 PWM output to go low. This
signals the channel-1 MOSFET driver to turn off the
channel-1 upper MOSFET and turn on the channel-1
synchronous MOSFET. If two-channel operation is selected,
the PWM2 pulse terminates 1/2 of a cycle later. If three
channels are selected the PWM2 pulse terminates 1/3 of a
cycle after PWM1, and the PWM3 output will follow after
another 1/3 of a cycle.
Once a channel’s PWM pulse terminates, it remains low for
a minimum of 1/4 cycle. This forced off time is required to
assure an accurate current sample as described in Current
Sensing. Following the 1/4-cycle forced off time, the
controller enables the PWM output. Once enabled, the PWM
output transitions high when the sawtooth signal crosses the
adjusted error-amplifier output signal, V
in Figures 1 and 5. This is the signal for the MOSFET driver
to turn off the synchronous MOSFET and turn on the upper
MOSFET. The output will remain high until the clock signals
the beginning of the next cycle by commanding the PWM
pulse to terminate.
CURRENT SENSING
Intersil multi-phase controllers sense current by sampling the
voltage across the lower MOSFET during its conduction
interval. MOSFET r
method to sense current for load-line regulation, channel-
current balance, module current sharing, and overcurrent
protection. If desired, an independent current-sense resistor
in series with the lower-MOSFET source can serve as a
sense element in place of the MOSFET r
DS(ON)
sensing is a no-added-cost
8
COMP
DS(ON).
as illustrated
The ISEN input for each channel uses a ground-referenced
amplifier to reproduce a signal proportional to the channel
current (Figure 4). After sufficient settling time, the sensed
current is sampled, and the sample is used for current
balance, load-line regulation and overcurrent protection. The
ISL6219 samples channel current once each cycle. Figure 4
shows how the sampled current, I
channel current I
current measurement and sampling circuitry for channel n in
an N-channel converter. This circuitry is repeated for each
channel in the converter but will not be active in unused
channels.
CHANNEL-CURRENT BALANCE
Another benefit of multi-phase operation is the thermal
advantage gained by distributing the dissipated heat over
multiple devices and greater area. By doing this, the
designer avoids the complexity of driving multiple parallel
MOSFETs and the expense of using expensive heat sinks
and exotic magnetic materials.
In order to fully realize the thermal advantage, it is important
that each channel in a multi-phase converter be controlled to
deliver about the same current at any load level. Intersil
multi-phase controllers guarantee current balance by
comparing each channel’s current to the average current
delivered by all channels and making an appropriate
adjustment to each channel’s pulse width based on the
error. Intersil’s patented current-balance method is
illustrated in Figure 5 where the average of the 2 or 3
sampled channel currents combines with the channel 1
sample, I
signal modifies the pulse width commanded by V
correct any unbalance and force I
In some circumstances, it may be necessary to deliberately
design some channel-current unbalance into the system. In
a highly compact design, one or two channels may be able
to cool more effectively than the other(s) due to nearby air
flow or heat sinking components. The other channel(s) may
SAMPLE
HOLD
FIGURE 4. INTERNAL AND EXTERNAL CURRENT-SENSING
ISL6219 INTERNAL CIRCUIT
&
I
n
I
1
SEN
, to create an error signal I
CIRCUITRY
=
I
L
L
. The circuitry in Figure 4 represents the
r DS ON
------------------------- -
+
R ISEN
-
(
)
ISEN(n)
EXTERNAL CIRCUIT
CHANNEL N
LOWER MOSFET
n
ER
, is created from the
R
ER
toward zero.
ISEN
. The filtered error
V
IN
+
CHANNEL N
UPPER MOSFET
-
I
L
COMP
r
DS ON
I
L
(
to
)