mc33192dw Freescale Semiconductor, Inc, mc33192dw Datasheet - Page 5
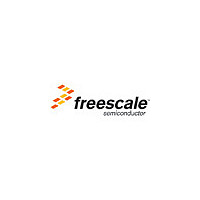
mc33192dw
Manufacturer Part Number
mc33192dw
Description
Mi-bus Interface Stepper Motor Controller
Manufacturer
Freescale Semiconductor, Inc
Datasheet
1.MC33192DW.pdf
(12 pages)
Available stocks
Company
Part Number
Manufacturer
Quantity
Price
Part Number:
MC33192DW
Manufacturer:
FREESCALE
Quantity:
20 000
not mutually exclusive; These are:
1) Noise Detection
Field message from the MCU twice for each Time Slot (t s )
of the Bi–Phase Code. A receive error occurs when the two
message samples fail to “logic wise” match. Noise and
Bi–Phase detection are discussed further under Message
Coding.
2) Bi–Phase Detection
message from the MCU detect the Bi–Phase Code. A
detector error occurs when the two time slots of the Bi–Phase
Code do not contain an Exclusive–OR logic function.
3) Field Check
contains an improper number of bits. A bit error can also be
detected by the MCU during the Push Field. The MCU can
simultaneously monitor the MI–Bus at the time it is sending
data. A bit error is detected if the sent bit value does not
match the value which was monitored.
4) Urgent Output Disable
device outputs will be disabled after a period of 9t s . The MCU
itself can take advantage of this feature to “globally” disable
the outputs of all system slave devices by keeping the
MI–Bus at a logic “0” level for a duration of 9t s or more.
Normal operation is resumed when the MCU sends a
“standard” instruction over the MI–Bus.
Basic Stepper Motor Construction and Operation
rotor magnetized with the same number of pole pairs as
contained in one stator coil section. Operationally, stepper
motors rotate at constant incremental angles by stepping one
step every time the current switches discretely in one stator
field coil causing the North–South stator field to rotate either
clockwise or counter–clockwise causing the permanent
magnet rotor to follow (see Figure 5). For simplicity, assume
the starting condition of the A1 to A2 stator field to be top to
bottom polarized N to S and the B1 to B2 stator field to be left
to right polarized N to S. The resulting stator field will produce
a vector which points in the direction of position 3. The rotor
will, in this case, be in the position shown in Figure 5 (pointing
to position 1). This initial condition corresponds to that of
step 1 in Figure 6. As the direction of current flow in the B1 to
B2 stator field is reversed, the field polarity of the B1 to B2
also reverses and is left to right polarized S to N. This causes
the resulting stator field vector to point in the direction of
position 4. This in turn causes the N–S rotor to follow and
rotate 90 in a clockwise direction and point in the direction of
position 2. This condition corresponds to step 2 of Figure 6.
Continued clockwise rotor steps will be experienced as the
stator field continues to be incrementally rotated as shown in
steps 3, 4, 5, etc. of Figure 6. The 90 steps in this simplistic
example constitute “full steps”. It is to be noticed that both
coils, in the foregoing full step example, were simultaneously
energized in one of two directions. It is possible to increment
the rotor in 45 “intermediate steps” or “half steps” by
alternately energizing only one stator coil at a time in the
appropriate direction while turning the other stator coil off.
The drive signals for Half Step operation are shown in
MOTOROLA ANALOG IC DEVICE DATA
There are four types of system error detections which are
The system MC33192 slave devices receive the Push
The system slave devices receiving the Push Field
A field error is detected when a fixed–form bit field
If the MI–Bus becomes shorted to ground, the slave
Stepper motors are constructed with a permanent magnet
MC33192
Figure 7. The Power output stages of the MC33192 consist
of two H–Bridges capable of driving two–phase bi–polar
permanent magnet motors in either half or full step
increment.
B1
(B1 to B2)
(A1 to A2)
Position
Direction
Coil B
Coil A
Rotor
Stator
Rotor
Step
Field
(A1 to A2)
(B1 to B2)
Direction
Figure 5. Permanent Magnet Stepper Motor
Position
Coil A
Stator
Rotor
Coil B
Rotor
Field
Step
2
3
Figure 6. 4–Step “Full Step” Operation
Figure 7. 8–Step “Half Step” Operation
+
+
–
–
+
–
+
–
CCW
1
CCW
1
A1
A2
2
2
3
3
4
5
4
6
7
5
4
1
8
CW
CW
6
1
5
B2