mc33192dw Freescale Semiconductor, Inc, mc33192dw Datasheet - Page 7
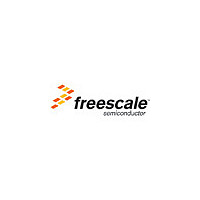
mc33192dw
Manufacturer Part Number
mc33192dw
Description
Mi-bus Interface Stepper Motor Controller
Manufacturer
Freescale Semiconductor, Inc
Datasheet
1.MC33192DW.pdf
(12 pages)
Available stocks
Company
Part Number
Manufacturer
Quantity
Price
Part Number:
MC33192DW
Manufacturer:
FREESCALE
Quantity:
20 000
MI–Bus Interface Description
single NPN transistor (Q1). The two main functions of this
NPN transistor are:
approximately 20 mA of current while also exhibiting low
saturation characteristics (V CE(sat) ).
any Electro–Magnetic Interference (EMI) captured on the
bus wire.
as a result of receiving excessive EMI energy present on the
bus. In addition, the transistor blocks the MCU from receiving
EMI signals which could erroneously change the data
direction register of the MCU I/O.
MI–Bus, is protected by two diodes (D2 and D3) and two
resistors (R5 and R6). Any transient EMI generated voltage
present on the bus is clamped by the two diodes to a
windowed voltage value not to be greater than the V DD or
less than the V SS supply voltages of the MCU.
MI–Bus Levels
recessive or dominant. The recessive state corresponds to a
Logic “1” and is obtained through use of a 10 k
resistor (R9) to 5.0 V. The dominant state corresponds to a
Logic “0” which represents a voltage less than 0.3 V and
created by the V CE(sat) of Q1.
MOTOROLA ANALOG IC DEVICE DATA
The MI–Bus Interface shown in Figure 9 is made up of a
1) To drive the MI–Bus during the Push Field with
2) To protect the Input/Output (I/O) pin of the MCU against
Without the NPN transistor, the MCU could be destroyed
The MCU input pin (P in ), used to read the Pull Field of the
The MI–Bus can have one of two valid logic states,
MCU
5.0 V
V DD
V SS
P out
P in
(10 k)
R5
R1
(4.7 K)
D1
V DD
Z1
(18 V)
D2
D3
Program
(3.9 k)
R3
(10 k)
Run
R4
(22 k)
R6
(1.2 k)
R2
Figure 9. MI–Bus MCU Interface
Q1
pull–up
MC33192
MI–Bus
Z in
MI–Bus Overvoltage Protection
interface circuit so as to protect the MCU output pin (P out )
from overvoltages commonly encountered in automotive
applications as a result of “Load Dump” and “Jump Start”
conditions. Load Dump is defined as the inductive transient
generated on the battery line as a result of opening the
battery connection while the alternator system is producing
charge current. Jump Start overvoltages are the result of
paralleling the installed automotive battery, through the use
of “jumper cables”, to an external voltage source in excess
of the vehicles nominal system voltage. For 12 V
automotive systems, it is common for 24 V “jump start”
voltages to be used.
load dump or jump start condition, the zener diode (Z1) is
activated and supplies base current to turn on the NPN
transistor Q1 causing the bus to be pulled to less than 0.3 V
producing a Logic “0” on the MI–Bus. After a duration
corresponding to 8t s (200 s) of continuous Logic “0” on the
bus all MC33192 devices will disable their outputs. Normal
operation is resumed, following the overvoltage, by the MCU
sending out a “standard” message instruction.
MI–Bus Termination Network
of MC33192 devices installed on the bus. Each MC33192
has an internal 10 k
pull–up resistor (R7) is recommended to be used to optimally
adjust termination of the bus for a load resistance of 600 .
5.0 V
An external zener diode (Z1) is incorporated in the
When an overvoltage situation (>18 V) exists, due to a
The MI–Bus is resistively loaded according to the number
R7
(1.2 k)
#2
#3
#4
#5
#6
#7
#8
1
Additional MC33192 Devices
(18 V)
(20 )
R8
Z2
5.0 V
pull–up resistor to 5.0 V. An external
R9
(10 k)
6.5 V
Q2
MC33192
Data
Out
7
2
V CC
Gnd
Programming
Data In
0 V
12 V
7