ATSAM3S-EK2 Atmel, ATSAM3S-EK2 Datasheet - Page 22
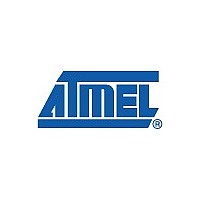
ATSAM3S-EK2
Manufacturer Part Number
ATSAM3S-EK2
Description
Development Boards & Kits - ARM EVAL KIT SAM3S8 & SAM3SD8 series
Manufacturer
Atmel
Datasheet
1.ATSAM3S-EK2.pdf
(35 pages)
Specifications of ATSAM3S-EK2
Rohs
yes
Product
Development Boards
Tool Is For Evaluation Of
SAM3SD8
Core
ARM
Interface Type
UART
Description/function
This kit lets designers quickly evaluate and develop code for applications running on Atmel SAM3S microcontrollers.
Processor Series
SAM3S
Factory Pack Quantity
1
Reliability Qualification and Monitoring
Overview and Philosophy
Reliability is the ability of a product to perform under stated conditions for a specified period of time. Generally, reliability
levels are expressed as the probability that a part will fail to function after a specified time interval. The same part will have
different probabilities of failure under different use conditions. For example, a part which may last for thirty years in
a desktop computer in an air-conditioned office building may last for only ten years in an underhood, automotive application
where temperature and humidity conditions are extreme.
In the electronics industry, this failure rate over time exhibits characteristics that, when summed, are commonly referred
to as the “Bathtub Curve”. This curve is typically divided into the three regions depicted below (Early Failure Rate,
Intrinsic Failure Rate, Wear Out Failure Rate).
As products can operate in a system for more than thirty years without failing, any test designed to accurately evaluate
reliability must utilize accelerated use conditions. This acceleration is achieved through the use of extreme environmental
(temperature, humidity, pressure) and operating (voltages, currents) conditions that serve to shorten the overall test
times to more manageable levels. Even under accelerated conditions, these tests may take several months to complete.
Long cycle times and high qualification costs have resulted in the emergence of techniques to evaluate reliability in wafer
form where even higher temperatures, voltages and currents can be applied for greater acceleration. These techniques
are referred to as Wafer Level Reliability (WLR).
Atmel
in our wafer fab areas. Further reliability enhancements are made by using packages and assembly subcontractors with
proven reliability and by qualifying these processes as well as products in packaged and finished forms before high volume
production release. Atmel’s Reliability Methodology consists of early evaluation and short-loop monitoring of its technologies
using wafer-level reliability (WLR), end-of-line reliability qualification of new products and technologies using a battery
of stress tests, and monitoring the reliability of production released products by periodically repeating these stress tests
on an ongoing basis. These three programs are referred to as Wafer Level Reliability (WLR), Reliability Qualification
Methodology, and Reliability Monitor Program.
Highly Accelerated Stress Test (HAST)
The purpose of this test is to evaluate a plastic packaged component’s ability to withstand harsh environmental conditions
with extreme temperature and humidity levels. The parts are stressed to high temperature (130°C) and relative
humidity (85%RH) conditions in a biased state to achieve maximum acceleration.
Atmel Quality Handbook
Failure
Rate
®
supplies the most reliable product to our customers by developing highly reliable technologies and design rules
Early
Failures
Intrinsic Failures
Time
Wear out
The specific shape and position of the bathtub curve is
dependent on the product design, material, processing
and defect density for both die and package. When
considering the overall reliability of the product, the
intended application(s) and the board/system level
manufacturing processes will contribute to the observed
reliability. As the knowledge and understanding of all
these factors grows, designs and processes can be
implemented and improved to ensure a robust and
reliable product.
22