MCZ33976EG Freescale Semiconductor, MCZ33976EG Datasheet - Page 33
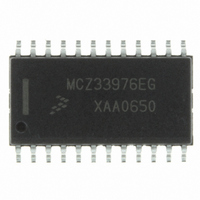
MCZ33976EG
Manufacturer Part Number
MCZ33976EG
Description
IC DRIVER DUAL GAUGE SPI 24-SOIC
Manufacturer
Freescale Semiconductor
Type
Serial Peripheral Interface (SPI) Dual Step Motor Gauge Driverr
Datasheet
1.MCZ33976EG.pdf
(41 pages)
Specifications of MCZ33976EG
Applications
Stepper Motor Driver, 2 Phase
Number Of Outputs
2
Current - Output
100mA
Voltage - Supply
6.5 V ~ 26 V
Operating Temperature
-40°C ~ 125°C
Mounting Type
Surface Mount
Package / Case
24-SOIC (7.5mm Width)
Supply Current
4 mA
Maximum Operating Temperature
+ 125 C
Mounting Style
SMD/SMT
Minimum Operating Temperature
- 40 C
Lead Free Status / RoHS Status
Lead free / RoHS Compliant
Voltage - Load
-
Lead Free Status / Rohs Status
Lead free / RoHS Compliant
Available stocks
Company
Part Number
Manufacturer
Quantity
Price
Part Number:
MCZ33976EG
Manufacturer:
FREESCALE
Quantity:
20 000
motor with the coils perfectly aligned at 90°, will vary little
from full step to full step if all other variables (e.g.,
temperature) are held constant. The full steps are evenly
spaced which results in equidistant movement as the motor
is full stepped.
angle will result in two distinct flux values as the coils are
driven in the same full step fashion. This lack of symmetry in
the measured flux is due to the difference in the electrical
angles between full steps. In other words, the distance that
the rotor moves changes from full step to full step. This
difference can be observed in
Figure
between alternating full steps (one coil at maximum current
while the other is at zero) is always six. In contrast, as seen
in
between full steps of the 60° coils alternates between four
and eight. These expected differences need to be taken into
account when setting the RTZ threshold.
position. The gauge not returning to zero can continue to be
controlled. An RTZ should not begin until the gauge to be
calibrated is at a static position and its pointer is at a full step
position. An attempt to calibrate a gauge while the other is in
the process of an RTZ event is ignored by the device. In most
applications of the RTZR command, it is possible to avoid a
visually obvious sequential calibration by first bringing the
pointers back close to their previous zero positions, then re-
calibrating them sequentially.
assigns the zero-step position to the full step position at the
end-stop location. Because the actual zero position could lie
anywhere within the full step where the zero was detected,
the assigned zero position could be within a window of ±0.5
degree. An RTZ can be used to detect stall, even if the
pointer already rests on the end stop when an RTZ sequence
is initiated. However, it is recommended the pointer be
advanced by at least 12 microsteps to the nearest full step
prior to initiating the RTZ.
RTZ OUTPUT
determine the state of the motor. The 33976 multiplexes the
coil voltages and provides the signal from the non-driven coil
to the RTZ pin.
DEFAULT MODE
internal or external reset prior to SPI communication. An
internal reset occurs during V
below 4.0 V. An external reset is initiated by the
driven to a logic [0]. With the exception of the RTZCR full step
time and the RMPSEL Register values, all of the specific pin
functions and internal registers will operate as though all of
the addressable configuration register bits were set to
logic [0]. This means, for example, all of the outputs will be
Analog Integrated Circuit Device Data
Freescale Semiconductor
Figure
It should be pointed out that the flux value, for an ideal
Only one gauge at a time can be returned to the zero
After completion of an RTZ, the 33976 automatically
During an RTZ event the non-driven coil is analyzed to
Default mode refers to the state of the 33976 after an
In comparison, motors that have coils aligned at a 60°
9, where PE6 = 0, the difference in microsteps
9, where PE6 = 1, the difference in microsteps
DD
Figure 9
power-up or if V
and
Table
RST
PWR
29. In
falls
pin
disabled after a power-up or external reset, and SO flag OD6
and OD8 are set, indicating an undervoltage event. Anytime
an external reset is exerted and the default is restored, all
configuration parameters (e.g., clock calibration, maximum
speed, RTZ parameters, etc.) are lost and must be reloaded.
FAULT LOGIC REQUIREMENTS
they occur:
of the SO pin with a valid SPI message.
likely an overcurrent condition will become a thermal issue
and be reported.
circuitry, which shuts off the affected gauge driver when
excessive temperatures are detected. In the event of a
thermal overload, the affected gauge driver is automatically
disabled. The overtemperature fault is flagged via the OT0
and/or OT1 device status bits. The indicating flag continues
to be set until the affected gauge is successfully re-enabled,
provided the junction temperature has fallen to a temperature
below the hysteresis level.
OVERVOLTAGE FAULT REQUIREMENTS
the maximum specified in
V
can result in uncertain pointer positions. Therefore, the
pointer position should be re-calibrated. The master will be
notified of an overvoltage event via the SO pin if the device
status is selected. Overvoltage detection and notification
occurs regardless of whether the gauge(s) are enabled or
disabled.
Overcurrent Fault Requirements
device to rely on thermal shutdown to protect itself.
Undervoltage Fault Requirements
pointer positions. Therefore, the internal clock and the pointer
position may require re-calibration. The state machine
continues with V
the coil voltages may be clipped. The master can be notified
of an undervoltage event via the SO pin.
RESET (SLEEP MODE)
level falls below the V
PWR
The 33976 device indicates each of the following faults as
•Overtemperature fault
•Undervoltage V
•Overvoltage V
•Clock out of spec
These fault bits remain enabled until they are clocked out
Overcurrent faults are not reported directly; however, it is
Overtemperature Fault Requirements
The 33976 incorporates overtemperature protection
The device is capable of surviving V
Output currents are limited to safe levels allowing the
Undervoltage V
The device can reset internally or externally. If the V
levels resulting in an Overvoltage Shutdown condition
PWR
PWR
PWR
PWR
voltage levels as low as 4.0 V; however,
DDUV
conditions may result in uncertain
LOGIC COMMANDS AND REGISTERS
Maximum Ratings
FUNCTIONAL DEVICE OPERATION
level (refer to the Static Electrical
PWR
voltages within
table, page 4.
DD
33976
33