TWR-56F8257 Freescale Semiconductor, TWR-56F8257 Datasheet - Page 73
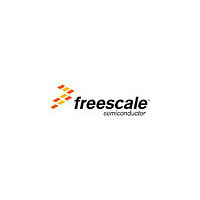
TWR-56F8257
Manufacturer Part Number
TWR-56F8257
Description
TOWER SYSTEM KIT MC56F8257
Manufacturer
Freescale Semiconductor
Type
DSC, Digital Signal Controllerr
Specifications of TWR-56F8257
Contents
Board, Cables, Documentation, DVD
For Use With/related Products
Freescale Tower System, MC56F8257
Lead Free Status / RoHS Status
Lead free / RoHS Compliant
value is closer to the application depends on the power dissipated by other components on the board. The value obtained on a
single layer board is appropriate for the tightly packed printed circuit board. The value obtained on the board with the internal
planes is usually appropriate if the board has low-power dissipation and the components are well separated.
When a heat sink is used, the thermal resistance is expressed as the sum of a junction-to-case thermal resistance and a
case-to-ambient thermal resistance.
where:
R
resistance, R
the mounting arrangement on printed circuit board, or the thermal dissipation on the printed circuit board surrounding the
device.
To determine the junction temperature of the device in the application when heat sinks are not used, the thermal characterization
parameter (
the package case. Refer to
where:
The thermal characterization parameter is measured per JESD51–2 specification using a 40-gauge type T thermocouple epoxied
to the top center of the package case. The thermocouple should be positioned so that the thermocouple junction rests on the
package. A small amount of epoxy is placed over the thermocouple junction and over about 1 mm of wire extending from the
junction. The thermocouple wire is placed flat against the package case to avoid measurement errors caused by cooling effects
of the thermocouple wire.
When heat sink is used, the junction temperature is determined from a thermocouple inserted at the interface between the case
of the package and the interface material. A clearance slot or hole is normally required in the heat sink. Minimizing the size of
the clearance is important to minimize the change in thermal performance caused by removing part of the thermal interface to
the heat sink. Because of the experimental difficulties with this technique, many engineers measure the heat sink temperature
and then back-calculate the case temperature using a separate measurement of the thermal resistance of the interface. From this
case temperature, the junction temperature is determined from the junction-to-case thermal resistance.
8.2
Freescale Semiconductor
JC
is device related and cannot be adjusted. You control the thermal environment to change the case to ambient thermal
Electrical Design Considerations
JT
CA
) can be used to determine the junction temperature with a measurement of the temperature at the top center of
. For instance, you can change the size of the heat sink, the air flow around the device, the interface material,
This device contains protective circuitry to guard against damage due to high static voltage
or electrical fields. However, take normal precautions to avoid application of any voltages
higher than maximum-rated voltages to this high-impedance circuit. Reliability of
operation is enhanced if unused inputs are tied to an appropriate voltage level.
Equation
R
R
R
CA
JA
JC
MC56F825x/MC56F824x Digital Signal Controller, Rev. 3
P
T
JT
T
D
5.
= Package junction-to-ambient thermal resistance (°C/W)
= Package junction-to-case thermal resistance (°C/W)
= Package case-to-ambient thermal resistance (°C/W)
= Thermocouple temperature on top of package (
= Thermal characterization parameter (
= Power dissipation in package (W)
T
R
J
JA
= T
= R
T
CAUTION
+ (
JC
JT
+ R
x P
CA
D
)
o
C/W)
o
C)
Design Considerations
Eqn. 4
Eqn. 5
73