PCF8576DT NXP Semiconductors, PCF8576DT Datasheet - Page 47
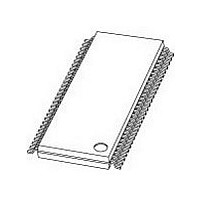
PCF8576DT
Manufacturer Part Number
PCF8576DT
Description
Manufacturer
NXP Semiconductors
Datasheet
1.PCF8576DT.pdf
(52 pages)
Specifications of PCF8576DT
Operating Supply Voltage (typ)
2.5/3.3/5V
Number Of Digits
20
Number Of Segments
160
Package Type
TSSOP
Pin Count
56
Mounting
Surface Mount
Power Dissipation
400mW
Frequency (max)
400KHz
Operating Supply Voltage (min)
1.8V
Operating Supply Voltage (max)
5.5V
Lead Free Status / Rohs Status
Supplier Unconfirmed
Available stocks
Company
Part Number
Manufacturer
Quantity
Price
Part Number:
PCF8576DT
Manufacturer:
NXP/恩智浦
Quantity:
20 000
Part Number:
PCF8576DT/2
Manufacturer:
NXP/恩智浦
Quantity:
20 000
NXP Semiconductors
19. Abbreviations
PCF8576D_9
Product data sheet
18.3.2 Quality of solder joint
18.3.3 Rework
18.3.4 Cleaning
The higher the stand off, the better the stresses are released due to TEC (Thermal
Expansion Coefficient) differences between substrate and chip.
A flip-chip joint is considered to be a good joint when the entire solder land has been
wetted by the solder from the bump. The surface of the joint should be smooth and the
shape symmetrical. The soldered joints on a chip should be uniform. Voids in the bumps
after reflow can occur during the reflow process in bumps with high ratio of bump diameter
to bump height, i.e. low bumps with large diameter. No failures have been found to be
related to these voids. Solder joint inspection after reflow can be done with X-ray to
monitor defects such as bridging, open circuits and voids.
In general, rework is not recommended. By rework we mean the process of removing the
chip from the substrate and replacing it with a new chip. If a chip is removed from the
substrate, most solder balls of the chip will be damaged. In that case it is recommended
not to re-use the chip again.
Device removal can be done when the substrate is heated until it is certain that all solder
joints are molten. The chip can then be carefully removed from the substrate without
damaging the tracks and solder lands on the substrate. Removing the device must be
done using plastic tweezers, because metal tweezers can damage the silicon. The
surface of the substrate should be carefully cleaned and all solder and flux residues
and/or underfill removed. When a new chip is placed on the substrate, use the flux
process instead of solder on the solder lands. Apply flux on the bumps at the chip side as
well as on the solder pads on the substrate. Place and align the new chip while viewing
with a microscope. To reflow the solder, use the solder profile shown in application note
AN10365 “Surface mount reflow soldering description” .
Cleaning can be done after reflow soldering.
Table 26.
Acronym
CMOS
CDM
HBM
ITO
LCD
LSB
MM
MSB
MSL
PCB
•
The bump height on the chip
Abbreviations
Description
Complementary Metal Oxide Semiconductor
Charged-Device Model
Human Body Model
Indium Tin Oxide
Liquid Crystal Display
Least Significant Bit
Machine Model
Most Significant Bit
Moisture Sensitivity Level
Printed Circuit Board
Rev. 09 — 25 August 2009
Universal LCD driver for low multiplex rates
PCF8576D
© NXP B.V. 2009. All rights reserved.
47 of 52