AD7858 Analog Devices, AD7858 Datasheet - Page 22
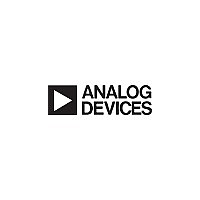
AD7858
Manufacturer Part Number
AD7858
Description
3 V to 5 V Single Supply, 200 kSPS, 8-Channel, 12-Bit, Serial Sampling ADC
Manufacturer
Analog Devices
Datasheet
1.AD7858.pdf
(32 pages)
Specifications of AD7858
Resolution (bits)
12bit
# Chan
8
Sample Rate
200kSPS
Interface
Ser,SPI
Analog Input Type
SE-Uni
Ain Range
(Vref) p-p,Uni (Vref)
Adc Architecture
SAR
Pkg Type
DIP,SOIC
Available stocks
Company
Part Number
Manufacturer
Quantity
Price
Part Number:
AD7858AN
Manufacturer:
ADI/亚德诺
Quantity:
20 000
Part Number:
AD7858ARSZ
Manufacturer:
ADI/亚德诺
Quantity:
20 000
Part Number:
AD7858ARZ
Manufacturer:
ADI/亚德诺
Quantity:
20 000
Part Number:
AD7858BR-REEL
Manufacturer:
ADI/亚德诺
Quantity:
20 000
Part Number:
AD7858BRZ
Manufacturer:
ADI/亚德诺
Quantity:
20 000
AD7858/AD7858L
Figure 27 shows a system gain calibration (assuming a system
full scale greater than the reference voltage) where the analog
input range has been increased after the system gain calibration
is completed. A system full-scale voltage less than the reference
voltage may also be accounted for by a system gain calibration.
Finally in Figure 28 both the system offset and gain are ac-
counted for by the a system offset followed by a system gain
calibration. First the analog input range is shifted upwards by
the positive system offset and then the analog input range is
adjusted at the top end to account for the system full scale.
System Gain and Offset Interaction
The inherent architecture of the AD7858/AD7858L leads to an
interaction between the system offset and gain errors when a
system calibration is performed. Therefore, it is recommended
to perform the cycle of a system offset calibration followed by a
system gain calibration twice. Separate system offset and system
gain calibrations reduce the offset and gain errors to at least the
12-bit level. By performing a system offset CAL first and a
system gain calibration second, priority is given to reducing the
gain error to zero before reducing the offset error to zero. If the
system errors are small, a system offset calibration would be
performed, followed by a system gain calibration. If the system
errors are large (close to the specified limits of the calibration
range), this cycle would be repeated twice to ensure that the
offset and gain errors were reduced to at least the 12-bit level.
The advantage of doing separate system offset and system gain
calibrations is that the user has more control over when the
analog inputs need to be at the required levels, and the
CONVST signal does not have to be used.
Alternatively, a system (gain + offset) calibration can be
performed. It is recommended to perform three system (gain +
offset) calibrations to reduce the offset and gain errors to the
12-bit level. For the system (gain + offset) calibration priority is
given to reducing the offset error to zero before reducing the
gain error to zero. Thus if the system errors are small then two
MAX SYSTEM FULL SCALE
MAX SYSTEM FULL SCALE
SYS OFFSET
V
V
MAX SYSTEM OFFSET
IS
REF
IS
REF
SYS F.S.
SYS F.S.
IS
–1LSB
2.5% FROM V
2.5% FROM V
AGND
– 1LSB
AGND
5% OF V
ANALOG
RANGE
ANALOG
INPUT
RANGE
INPUT
REF
REF
REF
SYSTEM OFFSET
FOLLOWED BY
SYSTEM GAIN
CALIBRATION
CALIBRATION
SYSTEM GAIN
CALIBRATION
V
REF
MAX SYSTEM FULL SCALE
MAX SYSTEM FULL SCALE
+ SYS OFFSET
SYS OFFSET
V
V
IS
IS
REF
REF
MAX SYSTEM OFFSET
SYS F.S.
SYS F.S.
2.5% FROM V
2.5% FROM V
– 1LSB
– 1LSB
IS
AGND
AGND
5% OF V
ANALOG
ANALOG
RANGE
RANGE
INPUT
INPUT
REF
REF
REF
system (gain + offset) calibrations will be sufficient. If the sys-
tem errors are large (close to the specified limits of the calibra-
tion range) three system (gain + offset) calibrations may be
required to reduced the offset and gain errors to at least the 12-
bit level. There will never be any need to perform more than
three system (offset + gain) calibrations.
The zero scale error is adjusted for an offset calibration and the
positive full-scale error is adjusted for a gain calibration.
System Calibration Timing
The calibration timing diagram in Figure 29 is for a full system
calibration where the falling edge of CAL initiates an internal
reset before starting a calibration (note that if the part is in power-
down mode the CAL pulsewidth must take account of the power-up
time). If a full system calibration is to be performed in software
it is easier to perform separate gain and offset calibrations so
that the CONVST bit in the control register does not have to be
programmed in the middle of the system calibration sequence.
The rising edge of CAL starts calibration of the internal DAC
and causes the BUSY line to go high. If the control register is
set for a full system calibration, the CONVST must be used
also. The full-scale system voltage should be applied to the
analog input pins from the start of calibration. The BUSY line
will go low once the DAC and System Gain Calibration are
complete. Next the system offset voltage is applied to the AIN
pin for a minimum setup time (t
rising edge of the CONVST and remain until the BUSY signal
goes low. The rising edge of the CONVST starts the system
offset calibration section of the full system calibration and also
causes the BUSY signal to go high. The BUSY signal will go
low after a time t
plete. In some applications not all the input channels may be
used. In this case it may be useful to dedicate two input chan-
nels for the system calibration, one which has the system offset
voltage applied to it, and one which has the system full scale
voltage applied to it. When a system offset or gain calibration is
performed, the channel selected should correspond to the sys-
tem offset or system full-scale voltage channel.
The timing for a system (gain + offset) calibration is very similar
to that of Figure 29 the only difference being that the time t
will be replaced by a shorter time of the order of t
internal DAC will not be calibrated. The BUSY signal will
signify when the gain calibration is finished and when the part is
ready for the offset calibration.
CONVST (I/P)
BUSY (O/P)
CAL (I/P)
AIN (I/P)
CAL2
t
V
1
SYSTEM FULL SCALE
when the calibration sequence is com-
t
15
t
15
t
1
= 2.5 t
= 100ns MIN,
t
CAL1
CLKIN
SETUP
t
CAL2
t
SETUP
MAX,
t
= 13899
) of 100 ns before the
14
= 50/90ns MIN 5V/3V,
t
CAL1
t
CLKIN
= 111114 t
V
OFFSET
CAL2
t
16
t
CAL2
CLKIN
as the
,
CAL1