AD7858 Analog Devices, AD7858 Datasheet - Page 26
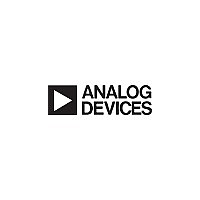
AD7858
Manufacturer Part Number
AD7858
Description
3 V to 5 V Single Supply, 200 kSPS, 8-Channel, 12-Bit, Serial Sampling ADC
Manufacturer
Analog Devices
Datasheet
1.AD7858.pdf
(32 pages)
Specifications of AD7858
Resolution (bits)
12bit
# Chan
8
Sample Rate
200kSPS
Interface
Ser,SPI
Analog Input Type
SE-Uni
Ain Range
(Vref) p-p,Uni (Vref)
Adc Architecture
SAR
Pkg Type
DIP,SOIC
Available stocks
Company
Part Number
Manufacturer
Quantity
Price
Part Number:
AD7858AN
Manufacturer:
ADI/亚德诺
Quantity:
20 000
Part Number:
AD7858ARSZ
Manufacturer:
ADI/亚德诺
Quantity:
20 000
Part Number:
AD7858ARZ
Manufacturer:
ADI/亚德诺
Quantity:
20 000
Part Number:
AD7858BR-REEL
Manufacturer:
ADI/亚德诺
Quantity:
20 000
Part Number:
AD7858BRZ
Manufacturer:
ADI/亚德诺
Quantity:
20 000
AD7858/AD7858L
CONFIGURING THE AD7858/AD7858L
The AD7858/AD7858L contains 14 on-chip registers which can
be accessed via the serial interface. In the majority of applications it
will not be necessary to access all of these registers. Here the
CLKIN signal is applied directly after power-on; the CLKIN
signal must be present to allow the part to perform a calibration.
This automatic calibration will be completed approximately 32 ms
after the AD7858 has powered up (4 MHz CLK).
For accessing the on-chip registers it is necessary to write to the
part. To change the channel from the default channel setting
the user will be required to write to the part. To enable Serial
Interface Mode 1 the user must also write to the part. Figure 34
and 35 outline flowcharts of how to configure the AD7858/
AD7858L Serial Interface Modes 1 and 2 respectively. The
continuous loops on all diagrams indicate the sequence for more
NOTE:
TWO SEPARATE WRITES ARE REQUIRED TO SET A NEW CHANNEL ADDRESS AND INITIATE A
CONVERSION ON THAT NEW CHANNEL IN SOFTWARE AS THE ACQUISITION TIME (2
MUST ELAPSE BEFORE THE CONVERSION BEGINS. IF BOTH COMMANDS ARE ISSUED IN THE ONE
WRITE THE RESULT OF THIS CONVERSION SHOULD BE DISCARDED AND THE NEXT
CONVERSION ON THAT SAME CHANNEL WILL PROVIDE CORRECT RESULTS.
PREVIOUS CONVERSION RESULT ON DIN PIN
APPLY SYNC (IF REQUIRED), SCLK, READ
TO CONTROL REGISTER SETTING CHANNEL
TO CONTROL REGISTER SETTING CONVST
APPLY SYNC (IF REQUIRED), SCLK, WRITE
CONVST RISING EDGE OR AFTER END
OF CONTROL REGISTER WRITE
WAIT APPROX. 200ns AFTER
BIT TO 1 (SEE NOTE)
TWO-WIRE MODE
WRITE
CURRENT CONVERSION RESULT ON DIN PIN
than one conversion. The options of using a hardware (pulsing
the CONVST pin) or software (setting the CONVST bit to 1)
conversion start, and reading/writing during or after conversion
are shown in Figures 34 and 35. If the CONVST pin is never
used then it should be tied to DV
ence is made to the BUSY bit equal to a Logic 0, to indicate the
end of conversion, the user in this case would poll the BUSY bit
in the status register.
Interface Mode 1 Configuration
Figure 34 shows the flowchart for configuring the part in Inter-
face Mode 1. This mode of operation can only be enabled by
writing to the control register and setting the 2/3 MODE bit.
Reading and writing cannot take place simultaneously in this
mode as the DIN pin is used for both reading and writing.
SETTING CHANNEL AND TWO-WIRE MODE
APPLY SYNC (IF REQUIRED), SCLK, READ
WAIT FOR AUTOMATIC CALIBRATION
POWER-ON, APPLY CLKIN SIGNAL,
WAIT FOR BUSY SIGNAL TO GO LOW
APPLY SYNC (IF REQUIRED), SCLK,
WRITE TO CONTROL REGISTER
YES
YES
WAIT FOR BUSY BIT = 0
PULSE CONVST PIN
CONVERSION
CONVERSION
INTERFACE
SOFTWARE
INITIATE
SERIAL
DURING
START
MODE
READ
DATA
OR
IN
?
?
?
1
NO
NO
t
CLKIN
)
DD
permanently. Where refer-