AN1231 Motorola / Freescale Semiconductor, AN1231 Datasheet
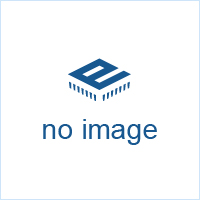
AN1231
Related parts for AN1231
AN1231 Summary of contents
Page 1
... Additionally, the JEDEC standard allows for any number of balls to be depopulated from a completely populated matrix (i.e, staggered pitch, corner, or center balls depopulated). A cross-sectional rendering of a typical PBGA mounted to a PCB is pictured in Figure 1. by AN1231/D AN1231 AN1231 1 ...
Page 2
... Table 2. Physical Properties of All Materials Used in the PBGA Package Modulus (ksi) Material Copper (ED/Rolled) 62% Sn/36% Pb/2% Ag Solder Dry Film soldermask BT/Glass Subtrate Silicon Die Mold Compound Ag Filled Epoxy Die Attach AN1231 2 many of the PBGA materials have a temperature-depen- dence that is not included in the table. Dimension (mil/mm) Comment 7.9/0.20 OR 15.7/0.40 BT/glass laminate core thickness. ...
Page 3
... Within this inner matrix, the centermost 9x9 pins form a ground bus and the remaining 40 pins encircle that with what is called a power ring. Those power and ground pins do not need to be AN1231 3 ...
Page 4
... Figure 2. Solder Pad for PBGA: a) recommended NSMD dumbbell pad shown with typical dimensions for most 1.27 mm pitch PBGAs, b) SMD dumbbell pad for most 1.27 mm pitch PBGAs, C) SMD teardrop pad, and d) NSMD pad as would be used for signal routing on the device layer of the motherboard. AN1231 4 rows in one direction further simplifies routing since there are a maximum of three buried rows ...
Page 5
... Voids form at the bottom (motherboard interface) of the ball, but end up at the joint/package interface due to buoyancy effects. These voids have been shown not reliability risk. Figure 4 shows a pad from an PBGA test board with b) 1.5/25 1.27/31 1.27/ AN1231 5 ...
Page 6
... The self-centering feature, which is a result of the surface tension Figure 4. Micrograph of an PBGA Test Board Pad with Eight Mils of Screenprinted Solder Paste (Magnification of Approximately 40X AN1231 6 of the molten solder, can be easily observed by placing de- vices deliberately off pad and reflowing. ...
Page 7
... Figure 6). More subtle joint assembly defects like voids, total wetting of the motherboard pad (i.e., full or partial opens) and solder splattering/balling require more sophisti- cated systems to detect. Very costly x-ray laminography sys- tems (i.e., Four Pi Systems) can detect such features AN1231 7 ...
Page 8
... A pad geometry design change that can allow detection of Figure 6. X-ray Micrograph of a Mounted PBGA Showing Solder Shorting Figure 7. X-ray Micrograph of a Mounted PBGA Showing Voiding in the Solder Joints AN1231 8 non-contact failures or opens involves modifying the mother- board pad footprint. A tab or ear is placed in the soldermask defined pad as in Figure 9 ...
Page 9
... The profile that is used to reflow the device should match the initial reflow profile as much as possible, although it is subject to the constraints previously discussed with regard to damaging neighboring devices. AN1231 9 ...
Page 10
... These test conditions are typically accelerated in cycle time as well as temperature extremes when compared to the actual application use environment. This is necessary since, by definition, an accelerated test is meant to decrease time AN1231 10 to failure so that the failure characteristics and mechanisms may be known before the prohibitive amount of time it would take for something to fail in an actual application ...
Page 11
... N Ò Ò Ò Ò Ò Ò Ò Ò Ö Ö Ö Ö Ö Ö P Ò Ò Ò Ò Ò Ò Ò Ò Ö Ö Ö Ö Ö Ö AN1231 11 ...
Page 12
... In this example the sample size was 28 and cycl- ing continued until all devices failed (100% device failure 0). Larger sample sizes such as these on the order greater are recommended. The and are determined by AN1231 12 CHAMBER AIR BOARD 100 ...
Page 13
... Weibull distribution. Which failure distribution is used ultimately depends on how it fits the majority of the collected data as well as the availability of statistical software and familiarity with a particular distribution 50% 7958 13.0 7737 0.965 NUMBER OF THERMAL CYCLES t i ( – – 0.042. The 10000 AN1231 13 ...
Page 14
... N xx%, xx%,ATC It has been proposed that a joint’s, and therefore the entire package’s, mean cycles to failure or N 50% follow a power law of the inelastic strain range seen by a joint during a thermal AN1231 50% 7628 0.042 0.985 NUMBER OF THERMAL CYCLES ...
Page 15
... Predicted Cycles to Failure Using: Devices Failed Devices Failed Per Million Weibull 1 2758 10 3291 0.01 100 3926 0.1 1000 4685 1.0 10,000 5592 10.0 100,000 6696 16.0 160,000 6960 50.0 500,000 7737 63.2 632,121 7958 Log Normal 4794 5035 5317 5659 6098 6739 6925 7628 7878 AN1231 15 ...
Page 16
... Another conclusion drawn from Motorola testing is that there is a relative cycle basis accel- eration factor of about 3.5 between 0 to 100 C and – 125 C PBGA testing. This actually results in no relative AN1231 16 Predicted N 0.1% (in Cycles) Using: Weibull 4685 ...
Page 17
... An example with a fracture approxi- mately one quarter of the way through the joint is presented in Figure 15. Figure 15. Micrograph of a 361 Pin PBGA Solder Joint Partial Fracture Surface After Application of Dye Penetrant Following 1885 –40 to 125 C Thermal Cycles (Magnification approximately 120X) 10.3 13.0 10.3 8.1 100000 AN1231 17 ...
Page 18
... Following this cold dwell, the devices are heated to the hot dwell where AN1231 18 they remain for another ten minutes. the system employs a circulating air environment to assure rapid stabilization at the specified temperature ...
Page 19
... August 1993, pp. 24 – 27. J. Vardaman, “Ball Grid Array Packaging”, TechSearch International, Inc. Consulting Report, January, 1993. W. Yip and C. Tsai, “Electrical Performance of an Over- molded Pad Array Carrier (OMPAC), 1993 International Electronics Packaging (IEPS) Conference Proceedings, pp. 731 – 739. AN1231 19 ...
Page 20
... SUMMARY OF JEDEC PLASTIC BALL GRID ARRAY FAMILY REGISTRATION 0.10 2. 2.50 MAX 2.15 NOM. 3.50 MAX SIDE VIEW ccc bbb C aaa C – C – A1 SEATING PLANE AN1231 20 APPENDIX A (Note: All Dimensions in mms ...
Page 21
... Maximum .15 .25 .35 .90 .70 AN1231 21 ...
Page 22
... PACKAGE MECHANICAL OUTLINES FOR THE 86, 119, 169, 225, 313, and 357 PIN PBGA B - -A- 0.20 (0.008 PIN 1A IDENTIFIER - -L- N TOP VIEW AN1231 22 APPENDIX B 86 PIN PBGA CASE 896A-01 0.20 (0.008) - ...
Page 23
... NOTES: 1. DIMENSIONING AND TOLERANCING PER ANSI Y14.5M, 1982. 2. CONTROLLING DIMENSION: MILLIMETER. MILLIMETERS INCHES DIM MIN MAX MIN MAX A 26.90 27.10 1.0590 1.0669 B 26.90 27.10 1.0590 1.0669 C 1.33 1.73 0.0523 0.0681 D 1.83 2.43 0.0720 0.0956 E 23.80 24.20 0.9370 0.9527 F 23.80 24.20 0.9370 0.9527 G 1.50 BSC 0.0590 BSC H 0.690 0.810 0.0271 0.0318 AN1231 23 ...
Page 24
... D 313X (SOLDER BALL) 0.300 (0.012 0.100 (0.004 VIEW F-F AN1231 24 313 PIN PBGA CASE 969A-01 DETAIL –B– 4X 0.200 (0.008 0.150 (0.006 ...
Page 25
... MILLIMETERS INCHES DIM MIN MAX MIN MAX A 25.00 BSC 0.984 BSC B 25.00 BSC 0.984 BSC C ––– 2.05 ––– 0.081 D 0.60 0.90 0.024 0.035 E 0.50 0.70 0.020 0.028 F 0.95 1.35 0.037 0.053 G 1.27 BSC 0.50 BSC K 0.70 0.90 0.028 0.035 N 22.40 22.60 0.882 0.890 P 22.40 22.60 0.882 0.890 R 22.86 BSC 0.900 BSC S 22.86 BSC 0.900 BSC AN1231 25 ...
Page 26
... SIGNAL PAD = POWER PAD = GROUND BUS AN1231 26 APPENDIX board with two signal, one power, and one ground plane. ...
Page 27
... MOTOROLA FAST SRAM BOTTOM LAYER METAL = 25 MIL VIA PAD = BOTTOMSIDE 8 MIL TRACE AN1231 27 ...
Page 28
... JAPAN: Nippon Motorola Ltd.: SPD, Strategic Planning Office, 4–32–1, Nishi–Gotanda, Shinagawa–ku, Tokyo 141, Japan. 81–3–5487–8488 ASIA/PACIFIC: Motorola Semiconductors H.K. Ltd.; 8B Tai Ping Industrial Park, MOS8 MOS8 T Pass/Fail Complete P Complete P Complete P Complete P Mfax is a trademark of Motorola, Inc. AN1231/D MOTOROLA FAST SRAM ...