AN1231 Motorola / Freescale Semiconductor, AN1231 Datasheet - Page 14
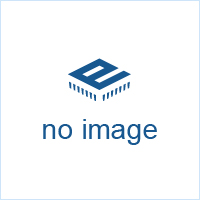
AN1231
Manufacturer Part Number
AN1231
Description
Plastic Ball Grid Array (PBGA)
Manufacturer
Motorola / Freescale Semiconductor
Datasheet
1.AN1231.pdf
(28 pages)
AN1231
14
Extrapolation to Application Failure Data
data and field failure data are usually different in three ways:
1) the sample size is much smaller in accelerated testing, 2)
the cycle duration is greater in the actual application and 3)
typical thermal excursions are usually less severe in the ap-
plication. Additionally, the isothermal temperature excursions
associated with thermal cycling are somewhat different than
the thermal gradients found in the mounted PBGA in an actu-
al application. The difference in the size of the population
(sample size) can generally be accounted for by extrapolat-
ing data from the previously mentioned statistical distribu-
tions. Due to the highly nonlinear dependence of PBGA
solder joint fatigue life on cycle time and severity, these dif-
ferences generally cannot be accounted for as simply. Typi-
cally, nonlinear finite element models employing the
viscoplastic temperature–dependent behavior of the solder
as it undergoes creep and plastic deformation must be used.
The finite element model is provided with accelerated testing
and field temperature distributions for a cycle and the solder
joint stress and inelastic strain or damage is determined.
Crack growth and S–N correlations may then be used to de-
termine the joint and subsequently the device life. The ratio
formed by dividing the percentage of the population failing
(N xx% ) in the field (f) by the accelerated thermal cycling
(ATC) testing cycles to failure is called the acceleration factor
(AF):
package’s, mean cycles to failure or N 50% follow a power law
of the inelastic strain range seen by a joint during a thermal
As mentioned previously, PBGA accelerated reliability
It has been proposed that a joint’s, and therefore the entire
95
90
80
70
60
50
40
30
20
10
5
2
1
1000
AF =
L/rr/c = fm–95
DISTRIBUTION
LOG NORMAL
N xx%,ATC
Figure 13. Log Normal Failure Distribution of the Data in Table 4
N xx%,f
N 50%
7628
0.042
NUMBER OF THERMAL CYCLES
(5)
R 2
0.985
AF
or application cycle (assuming inelastic strain is dominated
by creep as opposed to plastic deformation):
(see reference to Solomon in last section) to be approximate-
ly –2 for eutectic or near–eutectic solder. For long cycle dwell
times, as would be found in typical field applications, this
creep strain range is proportional to the cycle temperature
range ( T). This temperature range raised to the strain expo-
nent can then also be said to be proportional to the cycles to
failure. For accelerated reliability testing, this is not the case
unless the dwell times are sufficiently long to allow complete
stress relaxation in the joint as stresses are converted to
creep deformation. Substituting T for
both field and accelerated testing, substituting the resulting
equations into equation (5) and simplifying results yields an
equation of the form:
account for the field and ATC cyclic frequencies and maxi-
mum temperature seen during a cycle:
Where: f, ATC = Subscripts to indicate field and accelerated
The strain exponent (n) has been proposed by Solomon
This equation has been further modified in an attempt to
[
T ATC
f = Cyclic frequency (Note: For purposes of the
T max = Maximum temperature during a cycle ( K).
T f
T = Difference in minimum and maximum cyclic
thermal cycling testing.
extremes ( C).
above equation, f f minimum is 6 cycles per day).
–1.9
N 50%
f ATC
AF
f f
T
[
1/3
(
exp 1414
joint,inelastic ) n
T ATC
MOTOROLA FAST SRAM
T f
T max,f
– 2
1
10000
in equation (6) for
–
T max,ATC
1
(6)
(7)
(8)