AN1231 Motorola / Freescale Semiconductor, AN1231 Datasheet - Page 9
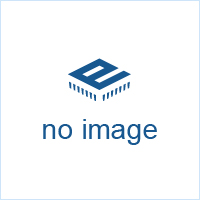
AN1231
Manufacturer Part Number
AN1231
Description
Plastic Ball Grid Array (PBGA)
Manufacturer
Motorola / Freescale Semiconductor
Datasheet
1.AN1231.pdf
(28 pages)
PBGA rework is that since the assembly process gives so
much better yields than high pin count, fine pitch leaded
devices, that the frequency of rework is greatly reduced. Un-
fortunately, when one joint is defective the entire package
must be replaced since there is no touchup. However,
methods and equipment do exist to successfully remove and
replace PBGA devices that are found to have assembly or
device-related defects.
DEVICE REMOVAL
above the liquidus temperature of the solder. As opposed to
the original surface mount assembly process, no special
considerations (assuming the device will be scrapped) need
to be taken with respect to ramp-up rates and time over soli-
dus as long as all joints are molten upon device lifting. It may
be beneficial to apply a liquid flux beneath the device prior to
heating and removal. This flux will facilitate uniform heating
and reduce device and board oxidation for subsequent sol-
dering processes. Joints which were not quite molten will ap-
pear as “candy kisses” on the board and PBGA after
removal. This is an indication that the device was removed at
the earliest possible time, such that the board is being sub-
jected to a minimal amount of temperature-induced damage.
If the assembled board has been exposed to out of dry-pack
conditions for an extended period of time (24 to 96 or more
hours depending on PBGA configuration and ambient condi-
tions) and removal is performed, “popcorning” or die attach
delamination may occur. To avoid this, the entire assembly
must be baked at 125 C for 12 hours. Since the saturation/
bake-out curves for PBGA are quite steep, baking for a half
to two-thirds of this time will go a long way in preventing pop-
corning as long as care is taken not to use an excessive
ramp-up rate (i.e., > 3 C/min) or maximum temperature
( 240 – 250 C).
devices) are proximate to the device being removed, care
must be taken not to overheat them and cause collateral
delamination damage. Studies performed by an equipment
division of Motorola who are a high volume PBGA user on
devices which have body sizes of 19 mm or less indicate that
neighboring devices should not exceed 185 C to prevent
popcorn at any reasonable saturation level. Also, to minimize
temperatures on adjacent devices the nozzle on the rework
station should be maintained around 100 mils from the top of
the PBGA and heating should be applied only from the top of
the device. Additionally, the size of the nozzle should be less
than or equal to the device molded body. As opposed to
leaded devices which require perimeter heating directly to
the leads, reflow of the PBGA is accomplished by heat con-
ducting through the body of the device. Heat can be applied
from the bottom also, but as stated earlier, this leads to
greater spreading of the heat and an increased chance of
damaging or partially reflowing neighboring devices if they
are present.
EQUIPMENT
devices, varies greatly with features. Some of the features
MOTOROLA FAST SRAM
The main point that should be stressed when discussing
Typically, PBGA device removal involves simply heating
If other known good PBGAs (or other surface mount
The cost of rework equipment for PBGA, as with leaded
REWORK AND REPAIR
that may be useful to include in rework stations for PBGA are
as follows: selectable top and/or bottom heating, selectable
IR and/or forced air heating, nitrogen capability, auto-profiling
capabilities, split-prism optics manual placement, automated
vision placement, and a device removal head or vacuum
tool. For the production rework of its smaller PBGA devices,
Motorola uses a simple, inexpensive (< $4K) portable rework
station made by A.P.E that provides top heating only and has
no device placement capabilities. Other PBGA users are
known to use the same industry-standard equipment they
use for their leaded device rework made by Conceptronics,
S.R.T., Air-Vac, Manix, and many others. Prices for these
latter machines are
vision placement capabilities. Of course, special PBGA-spe-
cific nozzles need to be bought or made for each of these
pieces of equipment. Due to their position as a supplier of
rework equipment to Motorola, A.P.E. has nozzles that cor-
respond to most current PBGA body sizes. As PBGA pop-
ularity increases, similar nozzles and related tooling will
undoubtedly be available from all rework equipment
suppliers.
PRE- AND POST-REWORK BOARD
CONSIDERATIONS
and subsequent replacement lies in the fact that the pad may
be soldermask defined and as such damage can occur if the
soldermask is subjected to extreme heat and/or has poor
initial adhesion to the copper pad. This situation is magnified
if the board technology is soldermask over solder (SMOS)
which is not recommended. If there are offset vias integral to
the tear-drop shaped PBGA pad and they are not filled or
tented with soldermask, the web between the usable pad
and via pad will be subjected to lifting due to its potential sub
10 mil width. Also, as with reworking all SMT device types,
the motherboard itself is subject to other modes of failure
such as blistering, delamination and copper/PCB adhesion
lifting if overheated or subjected to repeated heat cycles.
SITE PREPARATION AND DEVICE REPLACEMENT
quantity of solder remaining (approximately half of the ball
volume). This solder needs to be removed to allow device
placement and facilitate self aligning of the replacement
device. Removal can be performed with a solder sucker or
more manually with a solder wick. The site should be fluxed
prior to replacement with another PBGA device. Generally,
solder paste cannot be reapplied due to the interference of a
stencil and accompanying fixturing with other devices close
to the removal/replacement site. Short of machine replace-
ment with vision, the new device can be placed manually. A
board design consideration to aid in this can be a silk-screen
(assuming acceptable registration tolerance) or copper pat-
tern on the board that outlines the device body. Split prism
optics that allow viewing of the PBGA bump and solder pad
patterns simultaneously for alignment prior to device place-
ment are inexpensive and have been used very successfully.
The profile that is used to reflow the device should match the
initial reflow profile as much as possible, although it is
subject to the constraints previously discussed with regard to
damaging neighboring devices.
The principal board consideration during device removal
After device removal the pads will typically have a large
$40K and up without post-removal
AN1231
9