AN1231 Motorola / Freescale Semiconductor, AN1231 Datasheet - Page 5
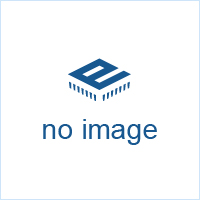
AN1231
Manufacturer Part Number
AN1231
Description
Plastic Ball Grid Array (PBGA)
Manufacturer
Motorola / Freescale Semiconductor
Datasheet
1.AN1231.pdf
(28 pages)
that it can typically be placed onto printed circuit boards and
assembled using existing surface mount equipment. This is
not true for many other new and high pin count packaging
technologies such as TAB, DCA, fine pitch QFPs, PGA, etc.
Most require new or upgraded process equipment and in
some cases new processes or manual assembly. It has the
added advantage of being compatible with existing handling
systems. Some pick and place equipment may require a vi-
sion system updgrade to recognize BGA balls. Open tooled
handling media, namely trays and tape and reel (heat seal or
C-pak) are available for many of the JEDEC PBGA body
sizes. Handling damage is significantly reduced by package
robustness due to the absence of fragile leads.
FLUXING/SCREEN PRINTING
spraying, dispensing, or foaming) must be applied to the PC
board solder pads prior to assembly. This is necessary to not
only reduce oxides formed on the solder pad, but also on the
solder ball. Slight solder ball oxidation may occur during ex-
posure to burn-in, storage, and dry baking in non-inert atmo-
spheres. Typically, the method chosen to apply flux is done
MOTOROLA FAST SRAM
One of the greatest advantages of the PBGA package is
Either solder paste (cream), paste flux or liquid flux (i.e.,
Ì Ì Ì Ì Ì Ì Ì Ì Ì Ì Ì Ì Ì Ì Ì Ì Ì Ì Ì Ì Ì Ì Ì Ì Ì Ì
Ì Ì Ì Ì Ì Ì Ì Ì Ì Ì Ì Ì Ì Ì Ì Ì Ì Ì Ì Ì Ì Ì Ì Ì Ì Ì
Ì Ì Ì Ì Ì Ì Ì Ì Ì Ì Ì Ì Ì Ì Ì Ì Ì Ì Ì Ì Ì Ì Ì Ì Ì Ì
Ì Ì Ì Ì Ì Ì Ì Ì Ì Ì Ì Ì Ì Ì Ì Ì Ì Ì Ì Ì Ì Ì Ì Ì Ì Ì
Ì Ì Ì Ì Ì Ì Ì Ì Ì Ì Ì Ì Ì Ì Ì Ì Ì Ì Ì Ì Ì Ì Ì Ì Ì Ì
SURFACE MOUNT ASSEMBLY
b) conventional non-soldermask defined pad. Note the greater volume of solder and greater
effective joint diameter for the non-soldermask defined pad to achieve the same stand-off.
Note: When encountered, fractions of traces were rounded down. Line spacing assumed to be equal to trace width.
Board Technology
Figure 3. Comparison of PBGA Solder Joints with: a) soldermask-defined pad and
Î Î Î Î Î Î Î Î Î
Î Î Î Î Î Î Î Î Î
Î Î Î Î Î Î Î Î Î
Î Î Î Î Î Î Î Î Î
Î Î Î Î Î Î Î Î Î
Î Î Î Î Î Î Î Î Î
Î Î Î Î Î Î Î Î Î
Î Î Î Î Î Î Î Î Î
Widths in Mils)
(Line/Space
(Line/Space
Î Î Î Î Î Î
Î Î Î Î Î Î
Î Î Î Î Î Î
Î Î Î Î Î Î
Table 3. Number of Escape Traces That Can Be Routed Between PBGA
Pads Given Device Pitch, Pad Diameter, and Board Line/Space Widths
3/3
4/4
5/5
6/6
8/8
a)
1.5/23
Number of Escape Traces Routed Between Pads Given Ball Pitch/Pad
5
4
3
2
1
Diameter (mms/mils). Shaded Columns Represent NSMD Pads.
1.5/25
5
3
2
2
1
1.5/31
4
3
2
1
1
Î Î Î Î Î Î Î Î Î Î
Î Î Î Î Î Î Î Î Î Î
Î Î Î Î Î Î Î Î Î Î
Î Î Î Î Î Î Î Î Î Î
Î Î Î Î Î Î Î Î Î Î
Î Î Î Î Î Î Î Î Î Î
Î Î Î Î Î Î Î Î Î Î
Î Î Î Î Î Î Î Î Î Î
Î Î Î Î Î Î Î Î Î Î
Î Î Î Î Î Î Î Î Î Î
to maintain compatibility with current processes. Due to the
fact that the solder ball is comprised of eutectic or near-eu-
tectic solder and its entire volume is molten during reflow, it is
not necessary to add solder volume to the joint with solder
paste. The 30 mil diameter ball provides enough volume to
give a 16 to 24 mil average stand-off across the device de-
pending on package and device/board solder pad configura-
tion. This is enough collapse to ensure that no opens will
occur due to device or board warpage at elevated tempera-
tures (more discussion on device warpage in the Coplanarity
section). Applying an amount of solder paste equal to 14% of
the ball volume (i.e., eight mil thick stencil, 25 mil diameter
apertures, final solder volume = 1/2 solder paste volume) will
generally increase the stand-off by one to two mils. In some
cases additional solder volume may be advantageous to
increase stand-off and subsequent device solder joint reli-
ability. However, applying larger amounts of solder paste with
the use of thicker stencils and/or larger apertures has the po-
tential to result in joint voiding, especially when combined
with fast oven ramp rates and volatile fluxes. Voids are
formed when flux volatilizes and is entrapped within the joint.
Voids form at the bottom (motherboard interface) of the ball,
but end up at the joint/package interface due to buoyancy
effects. These voids have been shown not to be a reliability
risk. Figure 4 shows a pad from an PBGA test board with
1.5/33
4
2
2
1
1
1.27/23
5
2
2
1
1
b)
1.5/25
3
2
2
1
1
1.27/31
2
1
1
1
1.27/33
2
1
1
AN1231
5