ADP3290JCPZ-RL ON Semiconductor, ADP3290JCPZ-RL Datasheet - Page 19
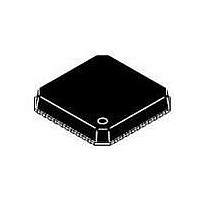
ADP3290JCPZ-RL
Manufacturer Part Number
ADP3290JCPZ-RL
Description
IC CTLR BUCK SW REG 40-LFCSP
Manufacturer
ON Semiconductor
Type
Step-Down (Buck)r
Datasheet
1.ADP3290JCPZ-RL.pdf
(30 pages)
Specifications of ADP3290JCPZ-RL
Internal Switch(s)
No
Synchronous Rectifier
Yes
Number Of Outputs
4
Voltage - Output
0.5 ~ 1.6 V
Frequency - Switching
250kHz ~ 4MHz
Voltage - Input
12V
Operating Temperature
0°C ~ 85°C
Mounting Type
Surface Mount
Package / Case
40-LFCSP
Output Voltage
0.5 V to 1.6 V
Output Current
500 uA
Input Voltage
- 0.3 V to + 6.3 V
Supply Current
25 mA
Switching Frequency
450 kHz
Mounting Style
SMD/SMT
Maximum Operating Temperature
+ 85 C
Minimum Operating Temperature
0 C
Lead Free Status / RoHS Status
Lead free / RoHS Compliant
Current - Output
-
Power - Output
-
Lead Free Status / Rohs Status
Lead free / RoHS Compliant
Available stocks
Company
Part Number
Manufacturer
Quantity
Price
the number of output capacitors. For this example, choosing
a 220 nH inductor is a good starting point and gives a
calculated ripple current of 12.5 A. The inductor should not
saturate at the peak current of 38.7 A and should be able to
handle the sum of the power dissipation caused by the
average current of 32.5 A in the winding and core loss.
resistance (DCR), which is used for measuring the phase
currents. A large DCR can cause excessive power losses,
though too small a value can lead to increased measurement
error. A good rule is to have the DCR (R
times the droop resistance (R
inductor with a DCR of 0.57 mW.
Designing an Inductor
to either design an inductor or to find a standard inductor that
comes as close as possible to meeting the overall design
goals. It is also important to have the inductance and DCR
tolerance specified to control the accuracy of the system.
Reasonable tolerances most manufacturers can meet are
15% inductance and 7% DCR at room temperature. The first
decision in designing the inductor is choosing the
core material. Several possibilities for providing low core
loss at high frequencies include the powder cores (from
Micrometals, Inc., for example, or Kool Mu® from
Magnetics®) and the gapped soft ferrite cores (for example,
3F3 or 3F4 from Philips®). Low frequency powdered iron
cores should be avoided due to their high core loss,
especially when the inductor value is relatively low and the
ripple current is high.
such as a potentiometer core (PQ, U, or E core) or toroid. A
good compromise between price and performance is a core
with a toroidal shape.
quickly designing a power inductor, such as:
•
•
Selecting a Standard Inductor
design consultation and deliver power inductors optimized
for high power applications upon request.
•
•
•
Current Sense Amplifier
measured at the CPU pins, to drop when the output current
The smallest possible inductor should be used to minimize
Another important factor in the inductor design is the dc
Once the inductance and DCR are known, the next step is
The best choice for a core geometry is a closed−loop type
Many useful magnetics design references are available for
The following power inductor manufacturers can provide
Most designs require the regulator output voltage,
Intusoft Magnetic Designer Software
Designing Magnetic Components for High Frequency
DC to DC Converters, by William T. McLyman,
Kg Magnetics, Inc., ISBN 1883107008
Coilcraft®
Coiltronics®
Sumida Corporation®
O
). This example uses an
L
) be about 1 to 1.5
http://onsemi.com
19
increases. The specified voltage drop corresponds to a dc
output resistance (R
ADP3290 has the flexibility of adjusting R
current limit or compensation components, and it can also
support CPUs that do not require a load line.
the CS amplifier (R
to the load line. All designs, whether they have a load line
or not, should keep R
across each inductor and passing the signal through a
low−pass filter. This summer filter is the CS amplifier
configured with resistors R
C
following equations, where R
inductors:
However, it is best to select R
solve for R
R
line.
that standard values can be used in parallel to get as close to
the desired value. For best accuracy, C
10% NPO capacitor. This example uses a 5% combination
for C
parallel. Recalculating R
combination yields 108.8 kW and 62 kW. The closest
standard 1% value for R
copper wire is used as the source of the DCR, the user needs
to compensate for temperature changes of the inductor’s
winding. Fortunately, copper has a well known temperature
coefficient (TC) of 0.39%/°C.
percentage change in resistance to that of the wire, it cancels
the temperature variation of the inductor DCR. Due to the
nonlinear nature of NTC thermistors, Resistor R
Resistor R
NTC and produce the desired temperature tracking.
CS
CSA
For designs requiring a load line, the impedance gain of
The output current is measured by summing the voltage
The user has the flexibility to choose either R
It is best to have a dual location for C
When the inductor DCR is used as the sense element and
If R
Next, use Equation 7 to solve for C
(filter). The impedance gain of the regulator is set by the
CS
= R
CS
of one 1.8 nF capacitor and one 1.5nF capacitor in
O
R
R
C
CS2
is designed to have an opposite and equal
= 1 mW because this is equal to the design load
PH(x)
PH(x)
CS
PH(X)
+
are needed. See Figure 10 to linearize the
+
+
0.57 mW
R
C
CSA
R
0.57 mW
O
1.0 mW
CSA
CS
by rearranging Equation 6. Here,
R
CSA
CSA
), also referred to as a load line. The
L
) must be to be greater than or equal
+
220 nH
PH(X)
+
CS
≥ 1 mW.
R
PH(X)
R
and R
L
R
R
PH(x)
CS
110 mW
CS
CS
is 61.9 kW.
L
L
110 kW + 63 kW
R
is the DCR of the output
equal to 110 kW, and then
PH(X)
(summers), and R
CS
R
CS
+ 35 nF
L
using this capacitor
CS
CS
should be a 5% or
O
.
, independent of
in the layout so
CS
or R
CS1
CS
(eq. 6)
(eq. 7)
PH(X)
and
and
.