LTC1871 Linear Technology, LTC1871 Datasheet - Page 14
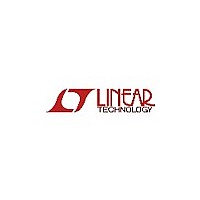
LTC1871
Manufacturer Part Number
LTC1871
Description
Wide Input Range/ No RSENSE Current Mode Boost/ Flyback and SEPIC Controller
Manufacturer
Linear Technology
Datasheet
1.LTC1871.pdf
(36 pages)
Available stocks
Company
Part Number
Manufacturer
Quantity
Price
Part Number:
LTC1871
Manufacturer:
LT/凌特
Quantity:
20 000
Company:
Part Number:
LTC1871EMS
Manufacturer:
LT
Quantity:
5 510
Part Number:
LTC1871EMS
Manufacturer:
LINEAR/凌特
Quantity:
20 000
Company:
Part Number:
LTC1871EMS#TRPBF
Manufacturer:
LT
Quantity:
4 500
Company:
Part Number:
LTC1871EMS-1
Manufacturer:
LT
Quantity:
10 000
Company:
Part Number:
LTC1871EMS-7
Manufacturer:
LT
Quantity:
10 000
Company:
Part Number:
LTC1871HMS
Manufacturer:
LT
Quantity:
10 000
Part Number:
LTC1871HMS
Manufacturer:
LINEAR/凌特
Quantity:
20 000
Part Number:
LTC1871IMS
Manufacturer:
LINEAR
Quantity:
20 000
APPLICATIO S I FOR ATIO
LTC1871
Remember that boost converters are not short-circuit
protected. Under a shorted output condition, the inductor
current is limited only by the input supply capability. For
applications requiring a step-up converter that is short-
circuit protected, please refer to the applications section
covering SEPIC converters.
The minimum required saturation current of the inductor
can be expressed as a function of the duty cycle and the
load current, as follows:
The saturation current rating for the inductor should be
checked at the minimum input voltage (which results in
the highest inductor current) and maximum output
current.
Boost Converter: Operating in Discontinuous Mode
Discontinuous mode operation occurs when the load
current is low enough to allow the inductor current to run
out during the off-time of the switch, as shown in Figure 9.
Once the inductor current is near zero, the switch and
diode capacitances resonate with the inductance to form
damped ringing at 1MHz to 10MHz. If the off-time is long
enough, the drain voltage will settle to the input voltage.
Depending on the input voltage and the residual energy in
the inductor, this ringing can cause the drain of the power
MOSFET to go below ground where it is clamped by the
body diode. This ringing is not harmful to the IC and it has
not been shown to contribute significantly to EMI. Any
attempt to damp it with a snubber will degrade the efficiency.
14
MOSFET DRAIN
I
INDUCTOR
L SAT
CURRENT
VOLTAGE
(
2A/DIV
2V/DIV
)
Figure 9. Discontinuous Mode Waveforms
V
V
IN
OUT
1
= 3.3V
= 5V
2
I
OUT
U
•
= 200mA
1
I
O MAX
–
(
D
U
2 s/DIV
MAX
)
W
1871 F09
U
Kool M is a registered trademark of Magnetics, Inc.
Boost Converter: Inductor Core Selection
Once the value for L is known, the type of inductor must be
selected. High efficiency converters generally cannot af-
ford the core loss found in low cost powdered iron cores,
forcing the use of more expensive ferrite, molypermalloy
or Kool M
size for a fixed inductor value, but is very dependent on the
inductance selected. As inductance increases, core losses
go down. Unfortunately, increased inductance requires
more turns of wire and therefore, copper losses will
increase. Generally, there is a tradeoff between core losses
and copper losses that needs to be balanced.
Ferrite designs have very low core losses and are preferred
at high switching frequencies, so design goals can con-
centrate on copper losses and preventing saturation.
Ferrite core material saturates “hard,” meaning that the
inductance collapses rapidly when the peak design current
is exceeded. This results in an abrupt increase in inductor
ripple current and consequently, output voltage ripple. Do
not allow the core to saturate!
Molypermalloy (from Magnetics, Inc.) is a very good, low
cost core material for toroids, but is more expensive than
ferrite. A reasonable compromise from the same manu-
facturer is Kool M .
Boost Converter: Power MOSFET Selection
The power MOSFET serves two purposes in the LTC1871:
it represents the main switching element in the power
path, and its R
ment for the control loop. Important parameters for the
power MOSFET include the drain-to-source breakdown
voltage (BV
resistance (R
gate-to-source and gate-to-drain charges (Q
respectively), the maximum drain current (I
the MOSFET’s thermal resistances (R
The gate drive voltage is set by the 5.2V INTV
regulator. Consequently, logic-level threshold MOSFETs
should be used in most LTC1871 applications. If low input
voltage operation is expected (e.g., supplying power from
®
DSS
cores. Actual core loss is independent of core
DS(ON)
DS(ON)
), the threshold voltage (V
) versus gate-to-source voltage, the
represents the current sensing ele-
TH(JC)
GS(TH)
and R
GS
D(MAX)
CC
), the on-
and Q
low drop
TH(JA)
) and
GD
).
,