lm2633mtd National Semiconductor Corporation, lm2633mtd Datasheet - Page 25
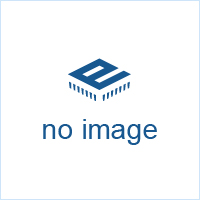
lm2633mtd
Manufacturer Part Number
lm2633mtd
Description
Advanced Two-phase Synchronous Triple Regulator Controller For Notebook Cpus
Manufacturer
National Semiconductor Corporation
Datasheet
1.LM2633MTD.pdf
(40 pages)
Design Procedures
ESR - Equivalent Series Resistance.
Loading transient - a load transient when the load current
goes from minimum load to full load.
Unloading transient - a load transient when the load current
goes from full load to minimum load.
C - regulator output capacitance.
D - duty cycle.
f - switching frequency.
I
I
I
I
I
ing a load transient, as derived from CPU specifications.
as specified by the CPU manufacturer.
L - inductance of the output inductor.
R
R
capacitors, as derived from CPU load transient specifica-
tions.
R
ing and Current Limiting .
t
t
during an unloading transient.
V
V
V
change.
V
V
General
Designing a power supply involves many tradeoffs. A good
design is usually a design that makes good tradeoffs. To-
day’s synchronous buck regulators typically run at a 200kHz
to 300kHz switching frequency. Beyond this range, switching
loss becomes excessive, and below this range, inductor size
becomes unnecessarily large. The LM2633 has a fixed op-
erating frequency of 250kHz when VIN voltage is below
about 17V, and has decreased frequency when VIN voltage
exceeds 17V. See Active Frequency Control section.
In a mobile CPU application, both the CPU core and the GTL
bus exhibit large and fast load current swings. The load
current slew rate during such a transient is usually well
beyond the response speed of the regulator. To meet the
regulation specification, special considerations should be
given to the component selection. For example, the total
combined ESR of the output capacitors must be lower than a
certain value. Also because of the tight regulation specifica-
tion, only a small budget can be assigned to ripple voltage,
typically less than 20mV. It is found that starting from a given
output voltage ripple will often result in fewer design itera-
tions.
±
±
nlim
ilim
irrm
load
rip
max
peak
V
I
in
n
old
new
rip
e
e_s
ilim
c_s
% - CPU core voltage regulation window.
% - LM2633 initial DAC tolerance.
c_s
- nominal output voltage.
- output inductor peak-to-peak ripple current.
- total combined ESR of output capacitors.
- input voltage to the switching regulators.
- ILIMx pin current.
- peak-to-peak output ripple voltage.
- maximum input current ripple RMS value.
- negative current limit level.
- load current.
- maximum allowed dynamic VID transition time.
- current limit adjustment resistance. See Current Sens-
- time for the CPU core voltage to reach its peak value
- maximum load current change during a load transient,
- maximum allowed total combined ESR of the output
- nominal CPU core voltage before dynamic VID
- nominal CPU core voltage after dynamic VID change.
- maximum allowed CPU core voltage excursion dur-
(Continued)
25
The design procedures that follow are generally appropriate
for both the CPU core and the GTL bus power supplies,
although emphasis is placed on the former. When there is a
difference between the two, it will be pointed out.
Output Capacitor Selection
Type of output capacitors
Different type of capacitors often have different combinations
of capacitance and ESR. High-capacitance multi-layer ce-
ramic capacitors (MLCs) have very low ESR, typically 12m ,
but also relatively low capacitance - up to 100µF. Tantalum
capacitors can have fairly low ESR, such as 18m , and
pretty high capacitance - up to 1mF. Aluminum capacitors
can have very high capacitance and fairly low ESR. OSCON
capacitors can achieve ESR values that are even lower than
those of MLCs’ while having a higher capacitance.
Tutorial on load transient response
Skip to the next subsection when a quick design is desired.
The control loop of the LM2633 can be made fast enough so
that when a worst-case load transient happens, duty cycle
will saturate (meaning it jumps to either 0% or D
control loop is fast enough, the worst situation for a load
transient will be that the transient happens when the follow-
ing three are also happening. One, present PWM pulse has
just finished. Two, input voltage is the highest. Three, the
load current goes from maximum down to minimum (referred
to as an unloading transient). Figure 2 shows how inductor
current changes during a worst-case load transient. The
reasons are as follows. In a mobile CPU application, the
input/output voltage differential, which is applied across the
inductor during a loading transient, is higher than the output
voltage, which is applied across the inductor during an un-
loading transient.
That means the inductor current changes slower during an
unloading transient than during a loading transient. The
slower the inductor current changes during a load transient,
the higher output capacitance is needed. That is why an
unloading transient is the worst case. If the load transient
happens when the present PWM pulse has just finished, the
inductor current will be the highest, which means highest
initial charging current for the output capacitors. Finally, the
higher the input voltage, the higher the inductor ripple cur-
rent and the higher the initial charging current for the output
capacitors.
FIGURE 2. Worst-case Load Transient
www.national.com
max
20000806
). If the