MAX15034BEVKIT+ Maxim Integrated Products, MAX15034BEVKIT+ Datasheet - Page 18
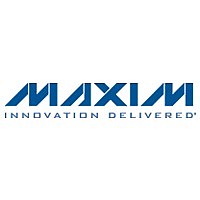
MAX15034BEVKIT+
Manufacturer Part Number
MAX15034BEVKIT+
Description
KIT EVALUATION FOR MAX15034
Manufacturer
Maxim Integrated Products
Specifications of MAX15034BEVKIT+
Main Purpose
DC/DC, Step Down
Voltage - Input
5 ~ 28V
Regulator Topology
Buck
Board Type
Fully Populated
Utilized Ic / Part
MAX15034
Lead Free Status / RoHS Status
Lead free / RoHS Compliant
Current - Output
-
Voltage - Output
-
Power - Output
-
Frequency - Switching
-
Outputs And Type
-
Lead Free Status / Rohs Status
Lead free / RoHS Compliant
The switching frequency per phase, peak-to-peak ripple
current in each phase, and allowable voltage ripple at
the output, determine the inductance value. Selecting
higher switching frequencies reduces the inductance
requirement, but at the cost of lower efficiency due to
the charge/discharge cycle of the gate and drain
capacitances in the switching MOSFETs. The situation
worsens at higher input voltages, since capacitive
switching losses are proportional to the square of the
input voltage. Lower switching frequencies on the other
hand increase the peak-to-peak inductor ripple current
(ΔI
losses (see the Power MOSFET Selection section for a
detailed description of MOSFET power loss).
When using higher inductor ripple current, the ripple can-
cellation in the multiphase topology, reduces the input
and output capacitor RMS ripple current. Use the follow-
ing equation to determine the minimum inductance value:
Choose ΔI
put current per channel. Since ΔI
ple voltage, the inductance value may need minor
adjustment after choosing the output capacitors for full-
rated efficiency. Choose inductors from the standard
high-current, surface-mount inductor series available
from various manufacturers. Particular applications may
require custom-made inductors. Use high-frequency core
material for custom inductors. High ΔI
peak-to-peak flux excursion increasing the core losses at
higher frequencies. The high-frequency operation cou-
pled with high ΔI
tance and even makes the use of planar inductors
possible. The advantages of using planar magnetics
include low-profile design, excellent current sharing
between phases due to the tight control of parasitics, and
low cost. For example, the minimum inductance at V
12V, V
The average current-mode control feature of the
MAX15034 limits the maximum inductor current, which
prevents the inductor from saturating. Choose an
inductor with a saturating current greater than the
worst-case peak inductor current:
Configurable, Single-/Dual-Output, Synchronous
Buck Controller for High-Current Applications
18
L
), and therefore, increase the MOSFET conduction
______________________________________________________________________________________
OUT
L
= 0.8V, ΔI
to be equal to approximately 30% of the out-
L
I
L PEAK
=
_
V
L
OUT IN MAX
, reduces the required minimum induc-
V
L
IN
(
=
= 3A, and f
V
×
24 75
(
f
Design Procedures
SW
.
R
SENSE
)
×
×
−
Δ
Inductor Selection
V
I
SW
10
L
L
OUT
affects the output-rip-
−
= 500kHz is 0.5μH.
3
)
+
L
Δ
2
I
causes large
L
IN
=
where 24.75mV is the maximum average current-limit
threshold for the current-sense amplifier and R
the sense resistor.
When choosing the MOSFETs, consider the total gate
charge, R
drain-to-source voltage, and package thermal imped-
ance. The product of the MOSFET gate charge and on-
resistance is a figure of merit, with a lower number
signifying better performance. Choose MOSFETs opti-
mized for high-frequency switching applications. The
average gate-drive current from the MAX15034’s output
is proportional to the total capacitance it drives at DH1,
DH2, DL1, and DL2. The power dissipated in the
MAX15034 is proportional to the input voltage and the
average drive current. See the Supply Voltage
Connections (V
Drives Supply (V
mum total gate charge allowed from all driver outputs
together.
The losses may be broken into four categories: conduc-
tion loss, gate drive loss, switching loss, and output loss.
The following simplified power loss equation is true for
both MOSFETs in the synchronous buck-converter:
For the low-side MOSFET, the P
virtually zero because the body diode of the MOSFET is
conducting before the MOSFET is turned on.
Tables 1 and 2 describe the different losses and shows
an approximation of the losses during that period.
The discontinuous input-current waveform of the buck
converter causes large ripple currents in the input
capacitor. The switching frequency, peak inductor cur-
rent, and the allowable peak-to-peak voltage ripple
reflected back to the source, dictate the capacitance
requirement. Increasing the number of phases increas-
es the effective switching frequency and lowers the
peak-to-average current ratio, yielding lower input
capacitance requirement. It can be shown that the
worst-case RMS current occurs when only one con-
troller section is operating. The controller section with
the highest output power needs to be used in determin-
ing the maximum input RMS ripple current requirement.
Increasing the output current drawn from the other out-
of-phase controller section results in reducing the input
P
LOSS
DS(ON)
=
IN
+
DD
P
, power dissipation, the maximum
/V
P
CONDUCTION
SWITCH
REG
) sections to determine the maxi-
Power MOSFET Selection
) and the Low-Side MOSFET
+
P
OUTP
Input Capacitance
+
SWITCH
P
GATEDRIVE
U U T
term becomes
SENSE
is