CES-A-BBA EUCHNER, CES-A-BBA Datasheet - Page 4
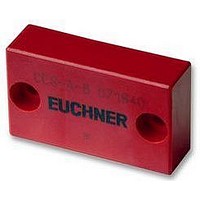
CES-A-BBA
Manufacturer Part Number
CES-A-BBA
Description
ACTUATOR
Manufacturer
EUCHNER
Datasheet
1.CES-A-BBA.pdf
(71 pages)
Specifications of CES-A-BBA
External Depth
40.5mm
External Length / Height
131mm
Operating Temperature Max
55°C
Operating Temperature Min
-0°C
Non-Contact Safety Switches CES/CEM
General information
According to EN 1088, interlocking devices are mechanical or
electrical devices which are designed to prevent the operation of
a machine element for as long as the movable safety guard is left
open.
Non-contact safety switches are interlocking devices which are
designed to protect people and machines.
Compared with electromechanical safety switches, they are used
if:
Functional description
The Coded Electronic Safety switch CES manufactured by
EUCHNER comprises three components:
The non-contact safety switches described here operate on the
basis of a uniquely electronically coded actuator (transponder).
The name transponder is a combination of the two terms
transmitter and responder.
The function of a transponder is easily explained: the transponder
(actuator) receives and processes the electromagnetic field from
a transceiver (read head), and the data signals are then sent back
to the receiver (evaluation unit) as a response depending on the
transponder coding.
This transponder technology has been used successfully in
electronic immobilizers for many years by almost all automotive
manufacturers.
Transponder technology is also used on the non-contact safety
switches series CES from EUCHNER and is an advanced solution
for a new safety concept.
Power is supplied and data transmitted to the coded actuator
using a non-contact, inductive read head. The major advantage of
the system is the battery-less actuator technology that will give
the user many years of service-free operation.
Every transponder is unique and absolutely secure against tampe-
ring.
The configuration of the system can be changed using a "teach-in
operation". In service new actuators can be taught very simply.
Each delivered actuator possesses a unique electronic coding
and so is a unique element in the system used. The code of the
actuator cannot be reprogrammed.
Signal transmission between the actuator and the read head is
achieved via a homogeneous field. It is permissible to rotate the
actuator within the operating distance of the read head.
4
Coded actuator
Read head
Evaluation unit
Subject to technical modifications; no responsibility is accepted for the accuracy of this information.
Thanks to the highly integrated circuits contained in the actuator
and the read head, switches with transponder technology can be
produced in units of virtually any tiny design.
EUCHNER also supplies read heads and actuators in rectangular
and circular designs, with or without plug connectors.
The read head is fastened to the fixed part of the safety guard
and is connected to the evaluation unit via a two-core screened
cable.
The actuator fastened to the safety guard is moved towards the
read head by closing the door. When the switch-on distance is
reached, power is supplied to the actuator by the inductive read
head and data can be transferred.
The bit pattern read is compared with the code saved in the
evaluation unit; if the data matches, the safety outputs are enabled
and the door monitoring output OUT (semiconductor output) is
also set HIGH.
Actuator and read head have a wide operating distance and a
broad hysteresis. Misalignment of the doors will not result in the
system switching off unintentionally. If, on the other hand, the
actuator is positioned exactly at the limit of the switch-on distance,
vibrations at the safety guard will not cause the machine to stop
unintentionally.
Polling of the read head, "actuator present," is single-channel and
dynamic. All potential faults (e.g. broken cable, short circuit, failure
of the actuator) are reliably detected. Thanks to the redundant,
diverse design of the evaluation unit in combination with two safety
outputs, the evaluation unit enters the safe state with every
detectable fault.
a high level of protection against tampering must be achieved
extremely hygienic environmental conditions are required (e.g.
in the food industry)
a precise door guide is not possible
machine doors are subjected to strong vibrations
a high safety category is determined in the risk analysis