TMC SIXPACK 2 TRINAMIC, TMC SIXPACK 2 Datasheet - Page 31
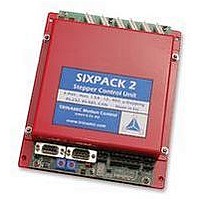
TMC SIXPACK 2
Manufacturer Part Number
TMC SIXPACK 2
Description
CONTROLLER, STEPPER MOTOR, AMPLIF
Manufacturer
TRINAMIC
Datasheet
1.TMC_SIXPACK_2.pdf
(48 pages)
Specifications of TMC SIXPACK 2
Supply Voltage Range
15Vdc To 48Vdc
No. Of Phases
Two
Output Current
1.4A
Approval Bodies
CE
Current Limit Max
1.4A
Current Limit Min
300mA
External Depth
35mm
External Length / Height
180mm
Svhc
No SVHC (15-Dec-2010)
Rohs Compliant
Yes
Lead Free Status / RoHS Status
Lead free / RoHS Compliant
th
SIXpack 2 – manual (V1.01 / May 5
, 2006) 31
6.6 Commands for axis movements
The SIXpack 2 provides different possibilities to move the axis. Which one to choose is related to the
demands of the application.
Basically there is the possibility to move the motor on the axis from a to b (ramps run) or with a fixed
velocity (rotation) until the next velocity command.
6.6.1 Basic ramp run
The ramp run requires the configuration of a reference run with the values for Poslimit, acceleration
and velocity (see CMD $15).
Through the command StartRamp, CMD $23 every position, defined by Poslimit can be achieved.
The target is defined by the variable TargetPosition (CMD $24, SQPack-tab “PI Controller”). The
motor is decelerated before it reaches the target position to stop at the exact target.
Figure 6.5: Schema of ramp generation
6.6.2 Start of constant rotation
For a rotation with a constant velocity the command ConstantRotation (CMD $25) transmits the variable
Velocity which defines the velocity for the constant move (calculation in 6.3).
After receiving the command the motor is accelerated with the maximum acceleration AMax until the
speed defined in Velocity is reached. To stop the axis the command ConstantRotation is used again
and Velocity is set to 0.
6.6.3 Change target position for ramp run
To change the target position of an active ramp run use the command SetTargetPosition (CMD $24,
SQPack-tab “PI Controller”) to transmit the variable TargetPosition with the new target of the
movement.
If the motor already reached its defined target SetTargetPosition takes no effect. To avoid failures and to
be sure the desired position is reached it is recommended to send the command StartRamp (CMD $23)
with the actual target position in addition afterwards. If the mode ConstantRotation (CMD $25) was
active, before, the motor is stopped and than moved to the target position.
6.6.4 Starting different motors synchronous
The command StartRampParallel (CMD $29) is used to start multiple ramp runs. Before this command is
sent each target position should be set with the command SetTargetPosition (CMD $24). When all
motors are inactive the parallel ramp run can be started.