AD9980KSTZ-80 Analog Devices Inc, AD9980KSTZ-80 Datasheet - Page 12
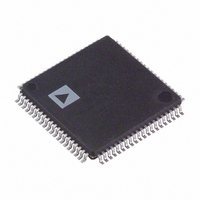
AD9980KSTZ-80
Manufacturer Part Number
AD9980KSTZ-80
Description
IC,Data Acquisition Signal Conditioner,3-CHANNEL,8-BIT,CMOS,QFP,80PIN,PLASTIC
Manufacturer
Analog Devices Inc
Datasheet
1.AD9980KSTZ-80.pdf
(44 pages)
Specifications of AD9980KSTZ-80
Applications
Video
Interface
Analog
Voltage - Supply
3.13 V ~ 3.47 V
Package / Case
80-LQFP
Mounting Type
Surface Mount
Lead Free Status / RoHS Status
Lead free / RoHS Compliant
For Use With
AD9980/PCBZ - KIT EVALUATION AD9980
Lead Free Status / RoHS Status
Lead free / RoHS Compliant
Available stocks
Company
Part Number
Manufacturer
Quantity
Price
Company:
Part Number:
AD9980KSTZ-80
Manufacturer:
ADI
Quantity:
830
Company:
Part Number:
AD9980KSTZ-80
Manufacturer:
Analog Devices Inc
Quantity:
10 000
Part Number:
AD9980KSTZ-80
Manufacturer:
ADI/亚德诺
Quantity:
20 000
AD9980
Negative target codes are included in order to duplicate a fea-
ture that is present with manual offset adjustment. The benefit
that is being mimicked is the ability to easily adjust brightness
on a display. By setting the target code to a value that does not
correspond to the ideal ADC range, the end result is an image
that is either brighter or darker. A target code higher than ideal
results in a brighter image while a target code lower than ideal
results in a darker image.
The ability to program a target code gives a large degree of
freedom and flexibility. While in most cases all channels will
be set to either 1 or 128, the flexibility to select other values
allows for the possibility of inserting intentional skews between
channels. It also allows the ADC range to be skewed so that
voltages outside of the normal range can be digitized. For
example, setting the target code to 40 allows the sync tip, which
is normally below black level, to be digitized and evaluated.
The internal logic for the auto-offset circuit requires 16 data
clock cycles to perform its function. This operation is executed
immediately after the clamping pulse. Therefore, it is important
to end the clamping pulse signal at least 16 data clock cycles
before active video. This is true whether using the AD9980’s
internal clamp circuit or an external clamp signal. The auto-
offset function can be programmed to run continuously or on a
one-time basis (see auto-offset hold, Register 0x2C, Bit 4). In
continuous mode, the update frequency can be programmed
(Register 0x1B, Bits [4:3]). Continuous operation with updates
every 64 Hsyncs is recommended.
A guideline for basic auto-offset operation is shown in Table 5
and Table 6.
Table 5. RGB Auto-Offset Register Settings
Register
0x0B
0x0C
0x0D
0x0E
0x0F
0x10
0x18, Bits [3:1]
0x1B, Bit [5:3]
Table 6. PbPr Auto-Offset Register Settings
Register
0x0B
0x0C
0x0D
0x0E
0x0F
0x10
0x18 Bits [3:1]
0x1B, Bit [5:3]
Value
0x02
0x00
0x02
0x00
0x02
0x00
000
110
Value
0x40
0x00
0x02
0x00
0x40
0x00
101
110
Comments
Sets red target to 4
Must be written
Sets green target to 4
Must be written
Sets blue target to 4
Must be written
Sets red, green, and blue
channels to ground clamp
Selects update rate and
enables auto-offset.
Comments
Sets Pr (red) target to 128
Must be written
Sets Y (green) target to 4
Must be written
Sets Pb (blue) target to 128
Must be written
Sets Pb, Pr to midscale clamp
and Y to ground clamp
Selects update rate and
enables auto-offset
Rev. 0 | Page 12 of 44
Sync-on-Green
The sync-on-green input operates in two steps. First, it sets a
baseline clamp level off of the incoming video signal with a
negative peak detector. Second, it sets the sync trigger level to
a programmable (Register 0x1D, Bits [7:3]) level (typically
128 mV) above the negative peak. The sync-on-green input
must be ac-coupled to the green analog input through its own
capacitor. The value of the capacitor must be 1 nF ±20%. If
sync-on-green is not used, this connection is not required. The
sync-on-green signal always has negative polarity.
Reference Bypassing
REFLO and REFHI are connected to each other through a
10 µF capacitor. REFCM is connected to ground through a
10 µF capacitor. These references are used by the input
PGA circuitry.
Clock Generation
A PLL is employed to generate the pixel clock. The Hsync input
provides a reference frequency to the PLL. A voltage controlled
oscillator (VCO) generates a much higher pixel clock
frequency. This pixel clock is divided by the PLL divide value
(Register 0x01 and Register 0x02) and phase-compared with
the Hsync input. Any error is used to shift the VCO frequency
and maintain lock between the two signals.
The stability of this clock is a very important element in
providing the clearest and most stable image. During each pixel
time, there is a period during which the signal is slewing from
the old pixel amplitude and settling at its new value. Then there
is a time when the input voltage is stable, before the signal must
slew to a new value (see Figure 6). The ratio of the slewing time
to the stable time is a function of the bandwidth of the graphics
DAC and the bandwidth of the transmission system (cable and
termination). It is also a function of the overall pixel rate.
Clearly, if the dynamic characteristics of the system remain
fixed, then the slewing and settling time is likewise fixed. This
time must be subtracted from the total pixel period, leaving the
stable period. At higher pixel frequencies, the total cycle time is
shorter and the stable pixel time also becomes shorter.
Figure 5. Input Amplifier Reference Capacitors
Figure 4. Typical Input Configuration
10µF
10µF
47nF
47nF
47nF
1nF
REFHI
REFLO
REFCM
R
B
G
SOG
AIN
AIN
AIN