PKS604PN Power Integrations, PKS604PN Datasheet - Page 14
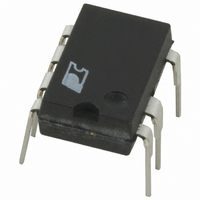
PKS604PN
Manufacturer Part Number
PKS604PN
Description
IC OFFLINE SWIT OTP OCP HV 8DIP
Manufacturer
Power Integrations
Series
PeakSwitch®r
Specifications of PKS604PN
Mfg Application Notes
PeakSwitch Design Guide AppNote
Output Isolation
Isolated
Frequency Range
250 ~ 304kHz
Voltage - Output
700V
Power (watts)
56W
Operating Temperature
-40°C ~ 150°C
Package / Case
8-DIP (0.300", 7.62mm), 7 Leads
Output Voltage
12 V
Input / Supply Voltage (max)
265 VAC
Input / Supply Voltage (min)
85 VAC
Duty Cycle (max)
65 %
Switching Frequency
47 KHz
Supply Current
25 uA
Operating Temperature Range
- 40 C to + 150 C
Mounting Style
Through Hole
For Use With
596-1126 - KIT DESIGN ACC PEAKSWITCH FAMILY
Lead Free Status / RoHS Status
Lead free / RoHS Compliant
Other names
596-1117-5
Available stocks
Company
Part Number
Manufacturer
Quantity
Price
Company:
Part Number:
PKS604PN
Manufacturer:
POWER
Quantity:
15 000
Part Number:
PKS604PN
Manufacturer:
POWER
Quantity:
20 000
of U
ripple voltage. AC feedback is provided directly through the
optocoupler with C
If necessary, a post filter (L
high frequency switching noise and ripple. Inductor L
be in the range of 1 µH – 3.3 µH with a current rating above the
peak output current. Capacitor C
100 µF to 330 µF with a voltage rating ≥1.25 × V
filter is used, the optcoupler should be connected (as shown in
Table 6) before the post filter inductor, and the sense resistors
after the post filter inductor (when applicable).
Design Tips
Overcurrent and Overvoltage Protection Circuits
In some applications, it may be necessary to protect the load in
fault conditions such as output overcurrent (OCP) or overvoltage
(OVP). For example, if the load is a motor, then OCP can
prevent the motor from overheating if it is stalled. Similarly,
if the feedback loop is opened then the load can be protected
from excessive voltage by overvoltage shutdown.
The smart AC sense feature of PeakSwitch simplifies
implementation of such protection by providing the latching
function on the primary side. Figure 15 shows a combined
overcurrent and overvoltage shutdown circuit. The circuit is
arranged so that if either overcurrent or overvoltage occurs,
then SCR Q2 is turned on, shorting the output. Normally, this
component would have to be sized to dissipate significant power.
However, when the arrangement is used with PeakSwitch,
the smart AC sense and latch-off feature will shut down the
supply.
For OCP, resistor R1 senses the output current, turning on
transistor Q1 when the voltage drop across R1 exceeds the
V
short term peak current but triggering the OCP in a true fault.
Resistor R3 limits the current into the gate of Q2.
For OVP, Zener diode VR1 is selected such that it conducts
when the output voltage exceeds the acceptable range, turning
on Q2. Resistor R4 limits the Zener current and determines
the turn-on point for Q2. Capacitor C2 provides decoupling,
preventing false triggering of Q2 due to noise.
Transistor Q1 can be any small signal PNP bipolar transistor. The
value of R1 is given by V
I
is the base-emitter drop of Q1. The initial values of R2 and C1
are selected such that 3τ ≥ t
minimum trip time in seconds. Use a starting value of 1 kW for R2,
then optimize based on measured trip time, as peak to continuous
current levels affect actual timing. Select R3 to exceed the worst
case gate trigger current of Q2, when Q1 conducts. Values of
1 kW to 4.7 kW are typical. Select the Zener voltage of VR1
Rev. E 02/07
OCP
14
BE
of Q1. Resistor R2 and C1 set a time constant allowing
FB2
where I
so that it does not respond to the cycle-by-cycle output
OCP
is the desired overcurrent trip point and V
AN-41
FB1
increasing the gain.
BE(Q1)
TRIP
PF
and C
where τ = R2 × C1 and t
/ I
OCP
PF
, and power rating V
PF
should be in the range of
) can be added to reduce
OUT
. If a post
PF
TRIP
should
BE(Q1)
is the
BE(Q1)
×
Figure 15. Example of Combined Secondary Over Current and
to be above the normal output voltage tolerance range,
including the tolerance of VR1 itself. Resistor R4 is a
0.25 W, 100 W part and C2 is a small, 100 nF ceramic. SCR Q2
should be selected with a current rating above the continuous
output current of the supply. For example for a 1 A output, a
2 A SCR would be a good choice. The anode of Q2 can be
directly connected to the anode of the output diode, so that
when fired, the secondary winding is shorted. This removes
the need for the SCR to discharge the output capacitor and may
allow a smaller current rating device to be selected. However,
an additional ultra-fast diode must be placed in series with the
SCR to block reverse current (see D10 in Figure 1).
In designs where the latching feature is not used, a larger current
rating SCR may be required.
Transformer Core Sizing
The high switching frequency of PeakSwitch allows the selection
of small core sizes that will adequately process the peak power.
However, the small core size reduces the amount of winding
window area available. This reduces the amount of copper for
the windings, increasing winding losses.
In designs where the ratio of peak to continuous power is low
(<~2), the transformer size may need to be increased to reduce
losses and transformer heating. Acceptable temperature rise
of the transformer should be verified at worst-case ambient
temperature and maximum load.
On-Time Extension
The on-time extension function of PeakSwitch maximizes the
power delivered to the load when the DC input (bulk capacitor)
voltage is low. This may allow the use of a smaller input
capacitor in designs where the output can droop under peak
load, especially in applications where the supply must pass
line brown-out or missing AC cycle tests. On-time extension
also increases the typical hold-up time.
Figure 16 is an example showing the effect of on-time extension
during a line brownout event.
Q
1
Overvoltage Protection Circuit.
C
1
R
R
R
1
2
3
R
4
VR1
PI-4340-031706
C
2
+V
Q
RTN
2
OUT