DS1874T+ Maxim Integrated Products, DS1874T+ Datasheet - Page 26
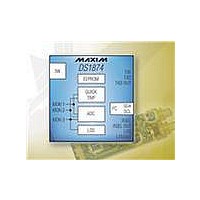
DS1874T+
Manufacturer Part Number
DS1874T+
Description
IC CTLR SFP+ ANLG LDD 28-TQFN
Manufacturer
Maxim Integrated Products
Type
Laser Diode Controllerr
Datasheet
1.DS1874TTR.pdf
(88 pages)
Specifications of DS1874T+
Number Of Channels
1
Voltage - Supply
2.85 V ~ 3.9 V
Current - Supply
2.5mA
Operating Temperature
-40°C ~ 95°C
Package / Case
28-WFQFN Exposed Pad
Mounting Type
Surface Mount
Number Of Outputs
5
Duty Cycle (max)
50 %
Output Voltage
0 V to 3.9 V
Mounting Style
SMD/SMT
Switching Frequency
0 KHz to 400 KHz
Operating Supply Voltage
2.85 V to 3.9 V
Supply Current
2.5 mA to 10 mA
Maximum Operating Temperature
+ 95 C
Fall Time
300 ns
Minimum Operating Temperature
- 40 C
Rise Time
300 ns
Synchronous Pin
Yes
Lead Free Status / RoHS Status
Lead free / RoHS Compliant
Other names
90-1874T+000
The following terminology is commonly used to
describe I
SFP+ Controller with Digital LDD Interface
Figure 17. I
26
SDA
SCL
NOTE: TIMING IS REFERENCED TO V
Master device: The master device controls the
slave devices on the bus. The master device gen-
erates SCL clock pulses and START and STOP
conditions.
Slave devices: Slave devices send and receive
data at the master’s request.
Bus idle or not busy: Time between STOP and
START conditions when both SDA and SCL are inac-
tive and in their logic-high states.
START condition: A START condition is generated
by the master to initiate a new data transfer with a
slave. Transitioning SDA from high to low while SCL
remains high generates a START condition. See
Figure 17 for applicable timing.
STOP condition: A STOP condition is generated by
the master to end a data transfer with a slave.
Transitioning SDA from low to high while SCL
remains high generates a STOP condition. See
Figure 17 for applicable timing.
Repeated START condition: The master can use a
repeated START condition at the end of one data
transfer to indicate that it will immediately initiate a
new data transfer following the current one.
Repeated STARTs are commonly used during read
______________________________________________________________________________________
STOP
2
2
t
BUF
C Timing
C data transfers.
START
t
HD:STA
IL(MAX)
t
I 2 C Communication
LOW
AND V
IH(MIN)
t
R
.
I
t
HD:DAT
2
C Definitions
t
HIGH
t
F
t
SU:DAT
REPEATED
operations to identify a specific memory address to
begin a data transfer. A repeated START condition
is issued identically to a normal START condition.
See Figure 17 for applicable timing.
Bit write: Transitions of SDA must occur during the
low state of SCL. The data on SDA must remain valid
and unchanged during the entire high pulse of SCL
plus the setup and hold time requirements (Figure
17). Data is shifted into the device during the rising
edge of the SCL.
Bit read: At the end a write operation, the master
must release the SDA bus line for the proper amount
of setup time (Figure 17) before the next rising edge
of SCL during a bit read. The device shifts out each
bit of data on SDA at the falling edge of the previous
SCL pulse and the data bit is valid at the rising edge
of the current SCL pulse. Remember that the master
generates all SCL clock pulses, including when it is
reading bits from the slave.
Acknowledgement (ACK and NACK): An acknowl-
edgement (ACK) or not acknowledge (NACK) is
always the ninth bit transmitted during a byte trans-
fer. The device receiving data (the master during a
read or the slave during a write operation) performs
an ACK by transmitting a zero during the ninth bit. A
device performs a NACK by transmitting a one dur-
ing the 9th bit. Timing (Figure 17) for the ACK and
NACK is identical to all other bit writes. An ACK is
the acknowledgment that the device is properly
receiving data. A NACK is used to terminate a read
START
t
SU:STA
t
HD:STA
t
SP
t
SU:STO