MC56F8367EVME Freescale Semiconductor, MC56F8367EVME Datasheet - Page 178
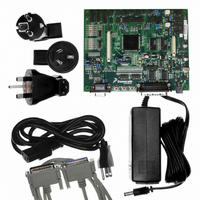
MC56F8367EVME
Manufacturer Part Number
MC56F8367EVME
Description
EVAL BOARD FOR MC56F83X
Manufacturer
Freescale Semiconductor
Type
DSPr
Specifications of MC56F8367EVME
Contents
Module and Misc Hardware
Processor To Be Evaluated
MC56F8145-67 and MC56F8345-67
Data Bus Width
16 bit
Interface Type
RS-232
Silicon Manufacturer
Freescale
Core Architecture
56800/E
Core Sub-architecture
56800/E
Silicon Core Number
MC56F
Silicon Family Name
MC56F83xx
Rohs Compliant
Yes
For Use With/related Products
MC56F83x5, MC56F83x6, MC56F83x7
Lead Free Status / RoHS Status
Lead free / RoHS Compliant
- Current page: 178 of 184
- Download datasheet (6Mb)
The thermal characterization parameter is measured per JESD51-2 specification using a 40-gauge type T
thermocouple epoxied to the top center of the package case. The thermocouple should be positioned so
that the thermocouple junction rests on the package. A small amount of epoxy is placed over the
thermocouple junction and over about 1mm of wire extending from the junction. The thermocouple wire
is placed flat against the package case to avoid measurement errors caused by cooling effects of the
thermocouple wire.
When heat sink is used, the junction temperature is determined from a thermocouple inserted at the
interface between the case of the package and the interface material. A clearance slot or hole is normally
required in the heat sink. Minimizing the size of the clearance is important to minimize the change in
thermal performance caused by removing part of the thermal interface to the heat sink. Because of the
experimental difficulties with this technique, many engineers measure the heat sink temperature and then
back-calculate the case temperature using a separate measurement of the thermal resistance of the
interface. From this case temperature, the junction temperature is determined from the junction-to-case
thermal resistance.
12.2 Electrical Design Considerations
Use the following list of considerations to assure correct operation:
178
•
•
•
•
•
•
Provide a low-impedance path from the board power supply to each V
from the board ground to each V
The minimum bypass requirement is to place six 0.01–0.1μF capacitors positioned as close as possible to
the package supply pins. The recommended bypass configuration is to place one bypass capacitor on each
of the V
performance tolerances.
Ensure that capacitor leads and associated printed circuit traces that connect to the chip V
pins are less than 0.5 inch per capacitor lead
Use at least a four-layer Printed Circuit Board (PCB) with two inner layers for V
Bypass the V
capacitor such as a tantalum capacitor
Because the device’s output signals have fast rise and fall times, PCB trace lengths should be minimal
DD
/V
DD
SS
This device contains protective circuitry to guard
against damage due to high static voltage or electrical
fields. However, normal precautions are advised to
avoid
maximum-rated voltages to this high-impedance circuit.
Reliability of operation is enhanced if unused inputs are
tied to an appropriate voltage level.
pairs, including V
and V
SS
application
layers of the PCB with approximately 100μF, preferably with a high-grade
SS
56F8367 Technical Data, Rev. 8
DDA
(GND) pin
/V
of
SSA.
CAUTION
Ceramic and tantalum capacitors tend to provide better
any
voltages
higher
DD
pin on the hybrid controller, and
than
DD
Freescale Semiconductor
and V
DD
SS
and V
Preliminary
SS
(GND)
Related parts for MC56F8367EVME
Image
Part Number
Description
Manufacturer
Datasheet
Request
R

Part Number:
Description:
56f8300 16-bit Digital Signal Controllers
Manufacturer:
Freescale Semiconductor, Inc
Datasheet:

Part Number:
Description:
Manufacturer:
Freescale Semiconductor, Inc
Datasheet:

Part Number:
Description:
Manufacturer:
Freescale Semiconductor, Inc
Datasheet:

Part Number:
Description:
Manufacturer:
Freescale Semiconductor, Inc
Datasheet:

Part Number:
Description:
Manufacturer:
Freescale Semiconductor, Inc
Datasheet:

Part Number:
Description:
Manufacturer:
Freescale Semiconductor, Inc
Datasheet:

Part Number:
Description:
Manufacturer:
Freescale Semiconductor, Inc
Datasheet:

Part Number:
Description:
Manufacturer:
Freescale Semiconductor, Inc
Datasheet:

Part Number:
Description:
Manufacturer:
Freescale Semiconductor, Inc
Datasheet:

Part Number:
Description:
Manufacturer:
Freescale Semiconductor, Inc
Datasheet:

Part Number:
Description:
Manufacturer:
Freescale Semiconductor, Inc
Datasheet:

Part Number:
Description:
Manufacturer:
Freescale Semiconductor, Inc
Datasheet:

Part Number:
Description:
Manufacturer:
Freescale Semiconductor, Inc
Datasheet:

Part Number:
Description:
Manufacturer:
Freescale Semiconductor, Inc
Datasheet:

Part Number:
Description:
Manufacturer:
Freescale Semiconductor, Inc
Datasheet: