FX1S-30MR-ES/UL MITSUBISHI, FX1S-30MR-ES/UL Datasheet - Page 227
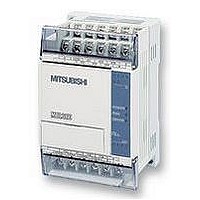
FX1S-30MR-ES/UL
Manufacturer Part Number
FX1S-30MR-ES/UL
Description
PLC, 16 IN, 14 RELAY OUT, 110V/2
Manufacturer
MITSUBISHI
Datasheet
1.FX1S-30MR-ESUL.pdf
(380 pages)
Specifications of FX1S-30MR-ES/UL
No. Of Analogue Inputs
16
No. Of Analogue Outputs
14
Ip/nema Rating
IP10
Approval Bodies
CE, CUL, UL
External Depth
49mm
External Length / Height
90mm
External Width
60mm
Mounting Type
Panel
- Current page: 227 of 380
- Download datasheet (7Mb)
FX Series Programmable Controlers
Configuring the PID loop
The PID loop can be configured to offer variations on PID control. These are as follows:
It should be noted that in all situations there must be a proportional or ‘P’ element to the loop.
P - proportional change
When a proportional factor is applied, it calculates the difference between the Current Error
Value, EV
fast the Process Value is moving closer to (or further away from) the Set Point Value NOT
upon the actual difference between the PV
Note: Other PID systems might operate using an equation that calculates the Proportional
change based upon the size of the Current Error Value only.
I - integral change
Once a proportional change has been applied to an error situation, ‘fine tuning’ the correction
can be performed with the I or integral element.
Initially only a small change is applied but as time increases and the error is not corrected the
integral effect is increased. It is important to note how T
integral correction is applied. The smaller T
Note: The T
Integral effect.
The Derivative Change
The derivative function supplements the effects caused by the proportional response. The
derivative effect is the result of a calculation involving elements T
error. This causes the derivative to initially output a large corrective action which dissipates
rapidly over time. The speed of this dissipation can be controlled by the value T
of T
Because the initial effect of the derivative can be quite severe there is a ‘softening’ effect which
can be applied through the use of K
considered as a filter allowing the derivative response to be scaled between 0 and 100%.
The phenomenon of chasing, or overcorrecting both too high and too low, is most often
associated with the Derivative portion of the equation because of the large initial correction
factor.
Note: The T
Derivative effect.
Control
method
D
PID
PD
PI
P
is small then the effect of applying derivative control is increased.
n
, and the Previous Error Value, EV
I
D
value is set in data register S
User value
User value
User value
User value
S
value is set in Data register S
3
+3 (K
Selection via setup registers
P
)
Set to 0 (zero)
Set to 0 (zero)
User value
User value
S
3
+ 4 (T
I
)
D
, the derivative gain. The action of K
nf
I
Set to 0 (zero)
Set to 0 (zero)
and SV.
3
n-1
is, the bigger effect the integral will have.
3
+4. Setting zero for this variable disables the
User value
S
User value
+6. Setting zero for this variable disables the
3
. The Proportional Change is based upon how
+ 6 (T
D
)
I
actually effects how fast the total
Proportional and derivative effect
Proportional and integral effect
Proportional effect only
D
, T
Description
S
Full PID
Applied Instructions 5
, and the calculated
5-105
D
: If the value
D
could be
Related parts for FX1S-30MR-ES/UL
Image
Part Number
Description
Manufacturer
Datasheet
Request
R

Part Number:
Description:
MITSUBISHI IGBT MODULES
Manufacturer:
MITSUBISHI
Datasheet:

Part Number:
Description:
MITSUBISHI INTELLIGENT POWER MODULES
Manufacturer:
MITSUBISHI
Datasheet:

Part Number:
Description:
TRANSFER-MOLD TYPE INSULATED TYPE
Manufacturer:
MITSUBISHI
Datasheet:

Part Number:
Description:
Manufacturer:
MITSUBISHI
Datasheet:

Part Number:
Description:
30A intelligent power module for flat-base type
Manufacturer:
MITSUBISHI
Datasheet:

Part Number:
Description:
15A - transistor module for medium power switching use, insulated type
Manufacturer:
MITSUBISHI
Datasheet:

Part Number:
Description:
5A power module for transfer-mold type insulated type
Manufacturer:
MITSUBISHI
Datasheet:

Part Number:
Description:
30A intelligent power module for flat-base type
Manufacturer:
MITSUBISHI
Datasheet:

Part Number:
Description:
TRANSFER-MOLD TYPE INSULATED TYPE
Manufacturer:
MITSUBISHI
Datasheet:

Part Number:
Description:
TRANSFER-MOLD TYPE INSULATED TYPE
Manufacturer:
MITSUBISHI
Datasheet:

Part Number:
Description:
20A - transistor module for medium power switching use, insulated type
Manufacturer:
MITSUBISHI
Datasheet:

Part Number:
Description:
20A - transistor module for medium power switching use, insulated type
Manufacturer:
MITSUBISHI
Datasheet: