FX1S-30MR-ES/UL MITSUBISHI, FX1S-30MR-ES/UL Datasheet - Page 228
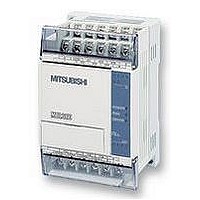
FX1S-30MR-ES/UL
Manufacturer Part Number
FX1S-30MR-ES/UL
Description
PLC, 16 IN, 14 RELAY OUT, 110V/2
Manufacturer
MITSUBISHI
Datasheet
1.FX1S-30MR-ESUL.pdf
(380 pages)
Specifications of FX1S-30MR-ES/UL
No. Of Analogue Inputs
16
No. Of Analogue Outputs
14
Ip/nema Rating
IP10
Approval Bodies
CE, CUL, UL
External Depth
49mm
External Length / Height
90mm
External Width
60mm
Mounting Type
Panel
- Current page: 228 of 380
- Download datasheet (7Mb)
FX Series Programmable Controlers
Effective use of the input filter
To prevent the PID instruction from reacting immediately and wildly to any errors on the
Current Value, there is a filtering mechanism which allows the PID instruction to observe and
account for any significant fluctuations over three samples.
The quantitative effect of the input filter is to calculate a filtered Input Value to the PID
instruction taken from a defined percentage of the Current Value and the previous two filtered
Input Values.
This type of filtering is often called first-order lag filter. It is particularly useful for removing the
effects of high frequency noise which may appear on input signals received from sensors.
The greater the filter percentage is set the longer the lag time. When the input filter is set to
zero, this effectively removes all filtering and allows the Current Value to be used directly as
the Input Value.
Initial values for PID loops
The PID instruction has many parameters which can be set and configured to the user’s
needs. The difficulty is to find a good point from which to start the fine tuning of the PID loop to
the system requirements. The following suggestions will not be ideal for all situations and
applications but will at least give users of the PID instruction a reasonable points from which to
start.
A value should be given to all the variables listed below before turning the PID instruction ON.
Values should be chosen so that the Output Manipulated Value does not exceed ± 32767.
Recommended initial settings:
T
5 times, etc.
K
to reach the set point - values should be experimented with from an arbitrary 75%
T
K
T
programmable controller reacts but also any valves, pumps or motors.
For a fast system reaction T
less than
beginning value can be
Care should be taken when adjusting PID variables to ensure the safety of the operator and
avoid damage to the equipment.
With ALL PID values there is a degree of experimentation required to tune the PID loop
to the exact local conditions. A sensible approach to this is to adjust one parameter at a
time by fixed percentages, i.e. say increasing (or decreasing) the K
10%. Selecting PID parameters without due consideration will result in a badly
configured system which does not perform as required and will cause the user to
become frustrated. Please remember the PID process is a purely mathematical
calculation and as such has no regard for the ‘quality’ of the variable data supplied by
the user/system - the PID will always process its PID mathematical function with the
data available.
On FX
PID process. Refer to page 10-28 for more details.
S
I
D
P
D
= This should ideally be 4 to 10 times greater than the T
= 50%
= Should be equal to the total program scan time or a multiple of that scan time, i.e. 2 times,
= This should be adjusted to a value dependent upon the maximum corrective action
= 50%
= This is set dependent upon the total system response, i.e. not only how fast the
2N
MPUs pre-tuning feature is available that can quickly provide initial values for the
T
S
. A slower reacting system will require the
T
D
D
will be set to a quick or small time, this should however
twice the value of T
S
3
+2
S
.
D
time
T
D
duration to be longer. A
Applied Instructions 5
P
value in steps of
5-106
never be
Related parts for FX1S-30MR-ES/UL
Image
Part Number
Description
Manufacturer
Datasheet
Request
R

Part Number:
Description:
MITSUBISHI IGBT MODULES
Manufacturer:
MITSUBISHI
Datasheet:

Part Number:
Description:
MITSUBISHI INTELLIGENT POWER MODULES
Manufacturer:
MITSUBISHI
Datasheet:

Part Number:
Description:
TRANSFER-MOLD TYPE INSULATED TYPE
Manufacturer:
MITSUBISHI
Datasheet:

Part Number:
Description:
Manufacturer:
MITSUBISHI
Datasheet:

Part Number:
Description:
30A intelligent power module for flat-base type
Manufacturer:
MITSUBISHI
Datasheet:

Part Number:
Description:
15A - transistor module for medium power switching use, insulated type
Manufacturer:
MITSUBISHI
Datasheet:

Part Number:
Description:
5A power module for transfer-mold type insulated type
Manufacturer:
MITSUBISHI
Datasheet:

Part Number:
Description:
30A intelligent power module for flat-base type
Manufacturer:
MITSUBISHI
Datasheet:

Part Number:
Description:
TRANSFER-MOLD TYPE INSULATED TYPE
Manufacturer:
MITSUBISHI
Datasheet:

Part Number:
Description:
TRANSFER-MOLD TYPE INSULATED TYPE
Manufacturer:
MITSUBISHI
Datasheet:

Part Number:
Description:
20A - transistor module for medium power switching use, insulated type
Manufacturer:
MITSUBISHI
Datasheet:

Part Number:
Description:
20A - transistor module for medium power switching use, insulated type
Manufacturer:
MITSUBISHI
Datasheet: